Brief
Executive Summary
- Sweeping market changes, capped by a pandemic, have made it clear that supply chains, long managed to be cost effective and reliable, now also must be resilient and sustainable.
- Resilient, sustainable supply chains offer a competitive advantage, but they require that companies have clear visibility throughout the chain and the ability to trace both inputs and outputs.
- The technology exists to do this, but companies must still figure out how to harvest and share data, which technologies to adopt for their business case, and how to use external certifications.
- Few, if any, companies can do this alone, but collaboration across an industry can help accelerate the effort.
Long before Covid-19, supply chains had been under increasing pressure from customers demanding customized, personalized products and immediate, inexpensive delivery. But most supply chains—built to deliver dependable supply at the lowest cost—weren’t up to those tasks. Many were stretched tautly across the globe even as rising trade tensions, market shocks, disruptive technologies, and the increasingly severe effects of climate change exposed them as brittle and opaque.
The pandemic, which ruptured so many of those chains, was merely a final blow. To executives, it already was clear that resilience—that is, a supply chain’s ability to heal, reroute or substitute inputs—had become as important as reliability and efficiency.
To make resilience a reality, however, executives need visibility into how materials and goods enter and move through the chain. They must be able to see what is happening everywhere in their supply chain and trace any item within it—from field to factory to customer and beyond. Today, the technology exists to turn that need into an operational reality.
Visibility and traceability also can help companies meet stakeholders’ growing demands for sustainable supply chains by making sure that sourcing raw materials, converting them into products and delivering them to market does no environmental, social or economic damage.
Both resilience and sustainability are priorities that executives can’t ignore. The pandemic highlighted the obvious dangers to any business with a supply chain that cannot operate in a crisis. But resilience also comes with huge benefits for companies that are able to continue serving their customers and to meet their increasingly changeable demands. Similarly, companies that lack sustainability can find their products penalized by regulators and scorned by customers, while companies that can point to sustainable practices and products are rewarded.
Balancing supply chain priorities
Of course, reliability and efficiency remain important priorities. But our recent survey of supply chain executives, conducted in collaboration with the World Economic Forum, shows that a new balance of priorities is emerging across industries: Both resilience and sustainability grew in importance, with sustainability boasting the highest percentage growth across industries over the past three years (see Figure 1).
The prioritization of resilience, sustainability and traditional supply chain priorities has become more balanced in recent years
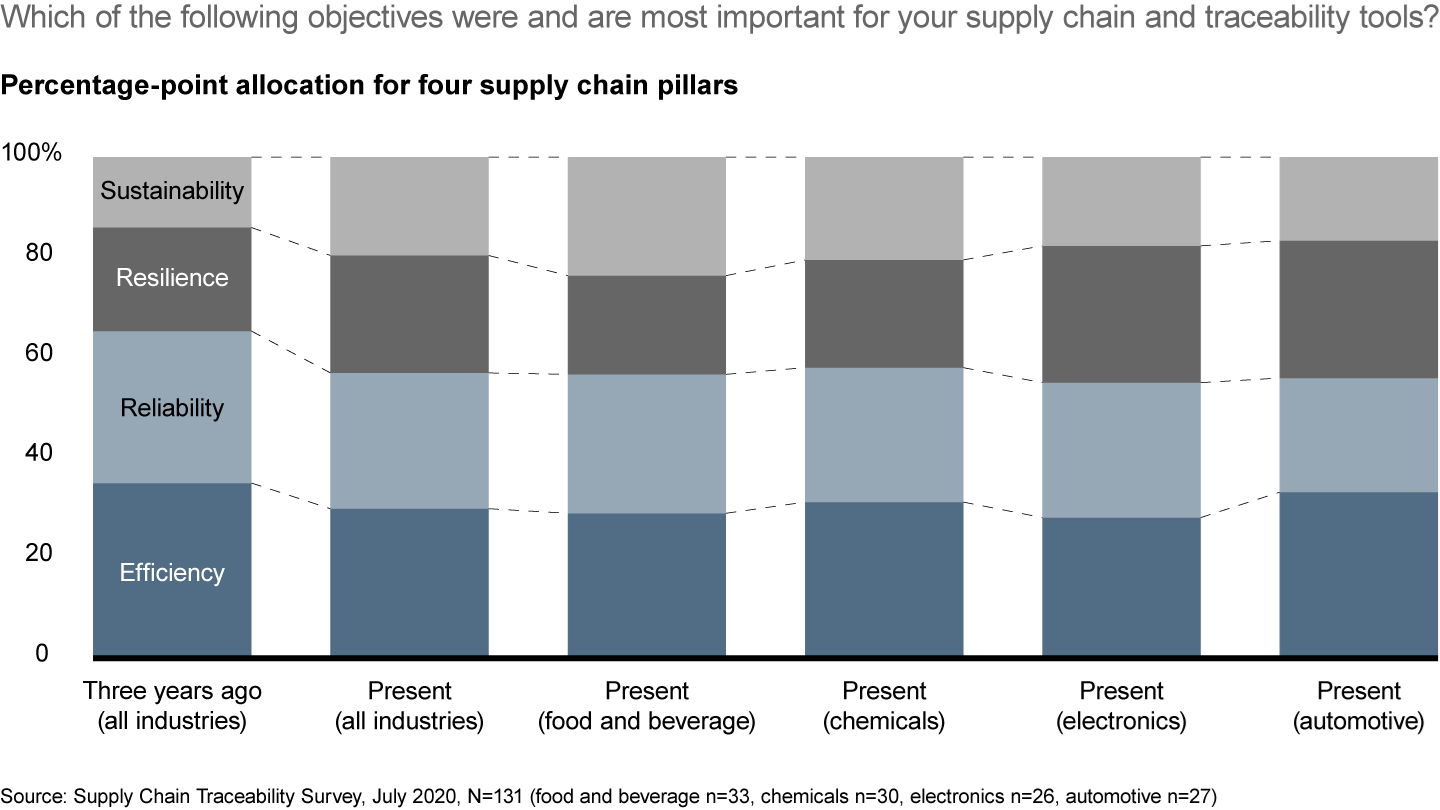
For years, supply chain executives tended to assume that resilience or sustainability require trade-offs on cost or dependability. And this is sometimes true. For example, a company that aims to increase resilience and reduce dependence on a single supplier by maintaining dual or multiple suppliers might need to pay a higher cost per unit.
But trade-offs are not a given, and often these priorities are complementary. Here, again, visibility and transparency play a key role, providing insights that can help executives make the best long- and short-term decisions. To do so, they need the right information at their fingertips from as far up and down the value chain as possible. For example, buying certified and sustainable inputs might be more expensive than noncertified ones, but companies often deliver premium economics through increased volume, market share gains and better pricing. Although many companies have been forced to seek greater visibility into their supply chains to increase resilience, those investments now can also reveal near-term opportunities to increase efficiency, reliability and sustainability. Across sectors, the companies that have the best visibility and traceability will have the most competitive supply chains (see Figure 2).
Visibility and traceability are at the heart of the supply chain of the future
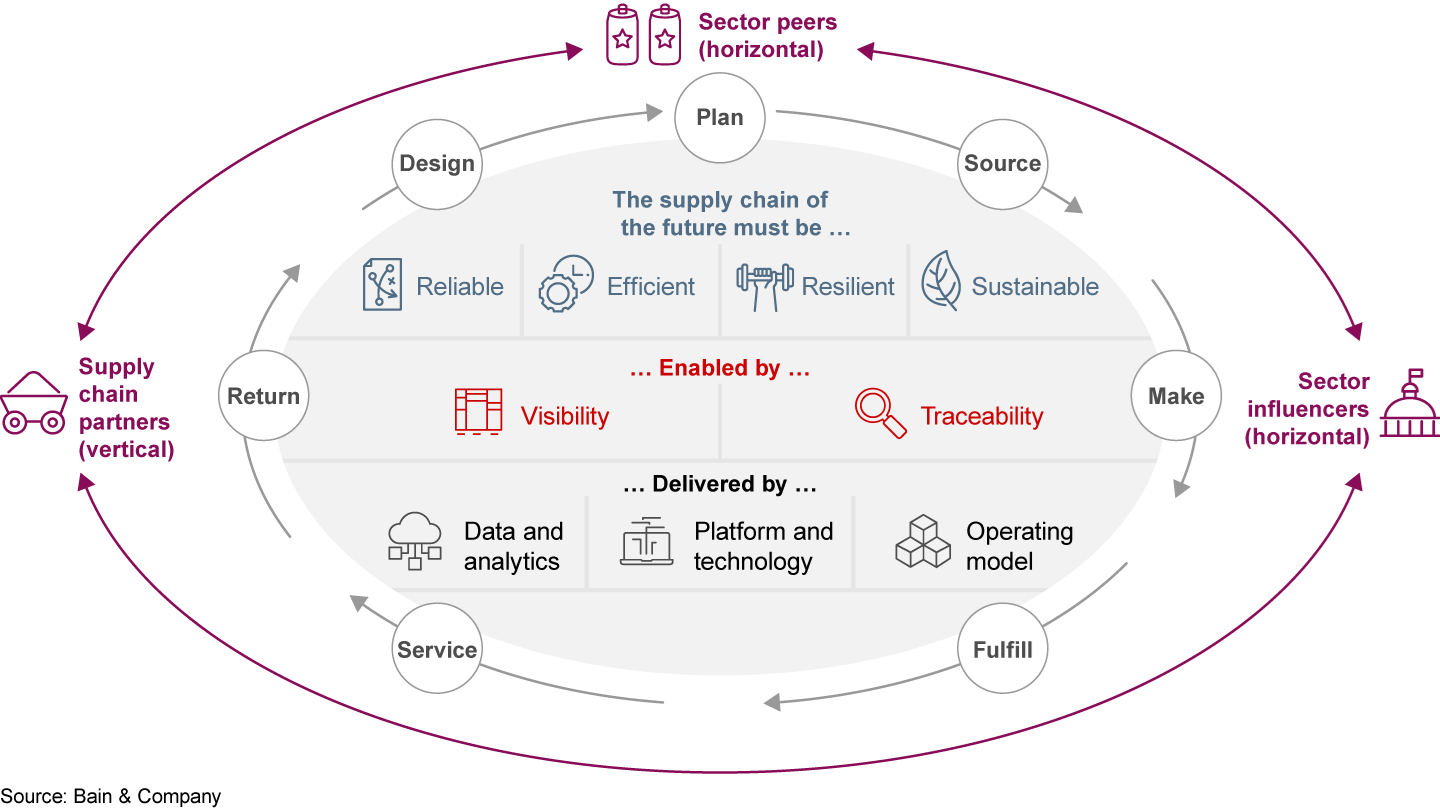
To achieve this, companies are adopting so-called “control towers,” with an ultimate goal of creating resilient, self-healing supply chains and seamless collaboration among the players along the chain. Technical sophistication ranges widely today:
- Some control towers provide real-time data across the full supply chain and can predict suboptimal events or disruptions.
- Many focus on limited portions of the supply chain, with batched data and less ability to predict.
- None yet have the deep transparency that industry-wide data standards and sharing would make possible. But we predict that day is not far off.
With the right data, control towers can provide much of the information needed to understand what’s happening within the supply chain—across supplier tiers, during the conversion process and all the way into the customers’ hands.
Managing the operations and economics of supply chains with the same tool used to manage sustainability, which was often not the direct responsibility of supply chain organizations in the past, also makes sustainability an integral part of overall supply chain decision making—both at the input level and during the conversion processes (see Figure 3).
Traceability allows organizations to embed sustainability directly into the supply chain decision-making process
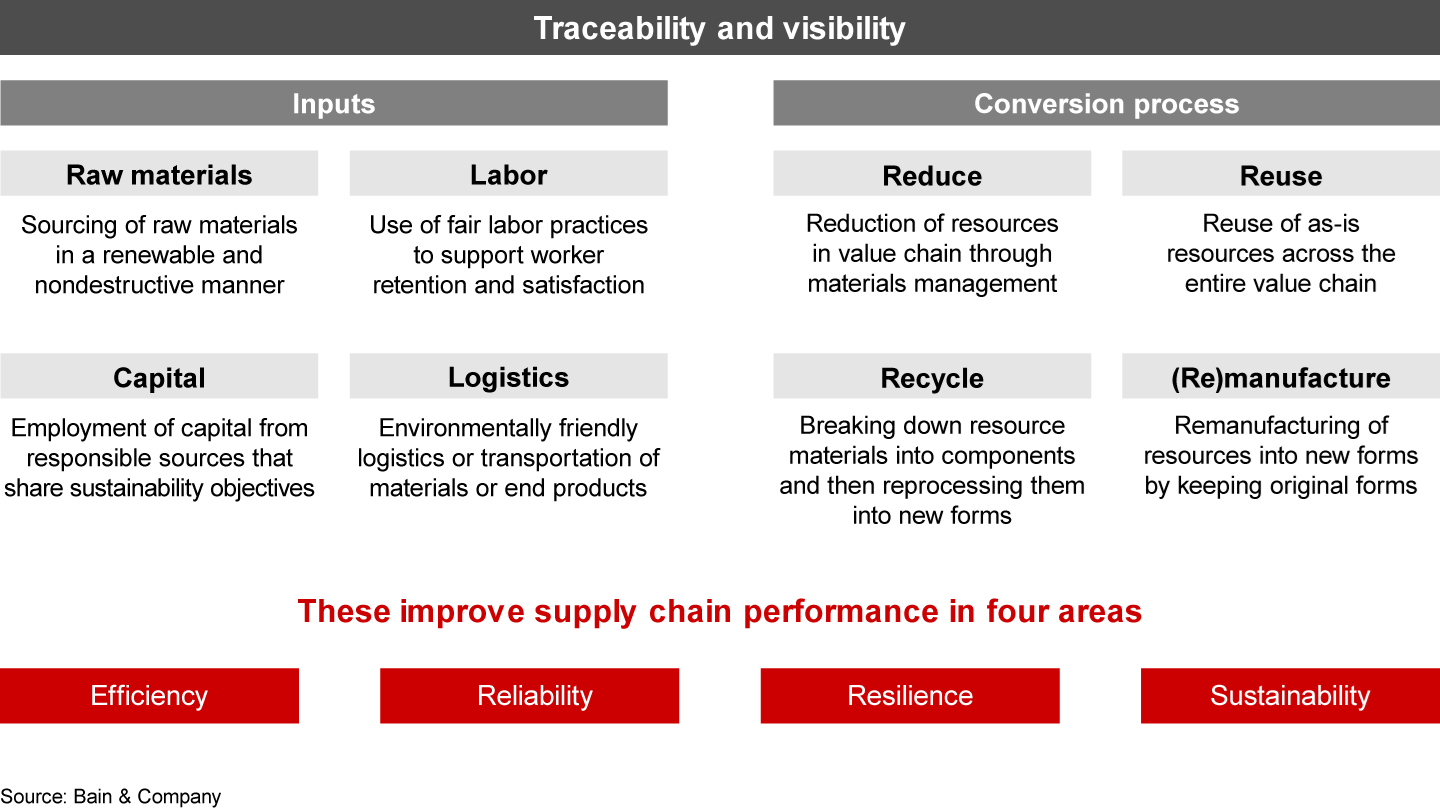
The increasing push for circular supply chains that recapture and reuse raw materials at the end of a product’s life cycle depends heavily on traceability. Tracing materials throughout the product life cycle is a prerequisite for feeding them back into the conversion process for reuse, recycling or remanufacturing. Each cycle reduces the consumption of raw input materials, and these circular supply chains are not limited to a single company’s value chain. Often, materials are recycled by third parties and later fed into another sector’s value chain as substitutes for virgin raw materials. To fully capture these opportunities, companies also need visibility into supply and demand.
Among many encouraging examples is the way in which Dole, the California-based agricultural multinational, has begun to incorporate advanced traceability solutions into its supply chain. Logging products on blockchain allows Dole to increase the efficiency of recalls and food safety investigations, and tracing a product now only takes seconds instead of weeks.
In the fashion world, LVMH announced the development, in partnership with ConsenSys and Microsoft, of AURA, a track-and-trace solution to prevent counterfeit products from entering the supply chain. Its vision is to share the product journey with consumers to instill trust in product authenticity and also to use the visibility into point-of-sale data to help better anticipate demand and prevent overproduction.
Cases such as these illustrate how supply chain traceability and visibility allow companies to deliver on their productivity, reliability, resilience and sustainability goals. As part of the World Economic Forum’s Accelerating Digital Traceability for Sustainable Production initiative, Bain gathered insights through interviews and surveys with more than 150 supply chain executives. Across companies and industries, respondents consistently reported a push for greater traceability and more reliable end-to-end supply chain visibility. Although all industries need efficient, resilient, reliable and sustainable supply chains, the specific business cases for traceability and visibility solutions tend to be industry specific (see the industry interactive below). This creates an opportunity for companies in the same industry to work together to tackle sector-wide challenges and to define their own traceability standards, but it also makes it more difficult to enable cross-sector solutions. The first movers within these industries will have the opportunity to set sustainability standards.
A path to achieving supply chain traceability and visibility
This is an exciting time for supply chain evolution. The availability of data continues to increase exponentially, and large-scale adoption of technologies such as artificial intelligence, the Internet of Things, blockchain and 5G makes it easier to gather relevant data in real time. This continuous stream of innovation makes a new level of supply chain transparency and sector-wide collaboration possible.
Still, fewer than 15% of executives feel as though their current capabilities allow them to deliver traceability consistently, according to the survey we conducted with the World Economic Forum. A majority of companies have started to build some capabilities, but in our survey, they gave their capabilities low marks for sophistication as they struggle to integrate them or realize business value. Unreliable or nonstandard data top their list of common barriers to traceability, with technical and organizational barriers close behind (see Figures 4 and 5). The journey toward traceable supply chains involves four key steps for companies.
Today’s traceability efforts still lack sophistication
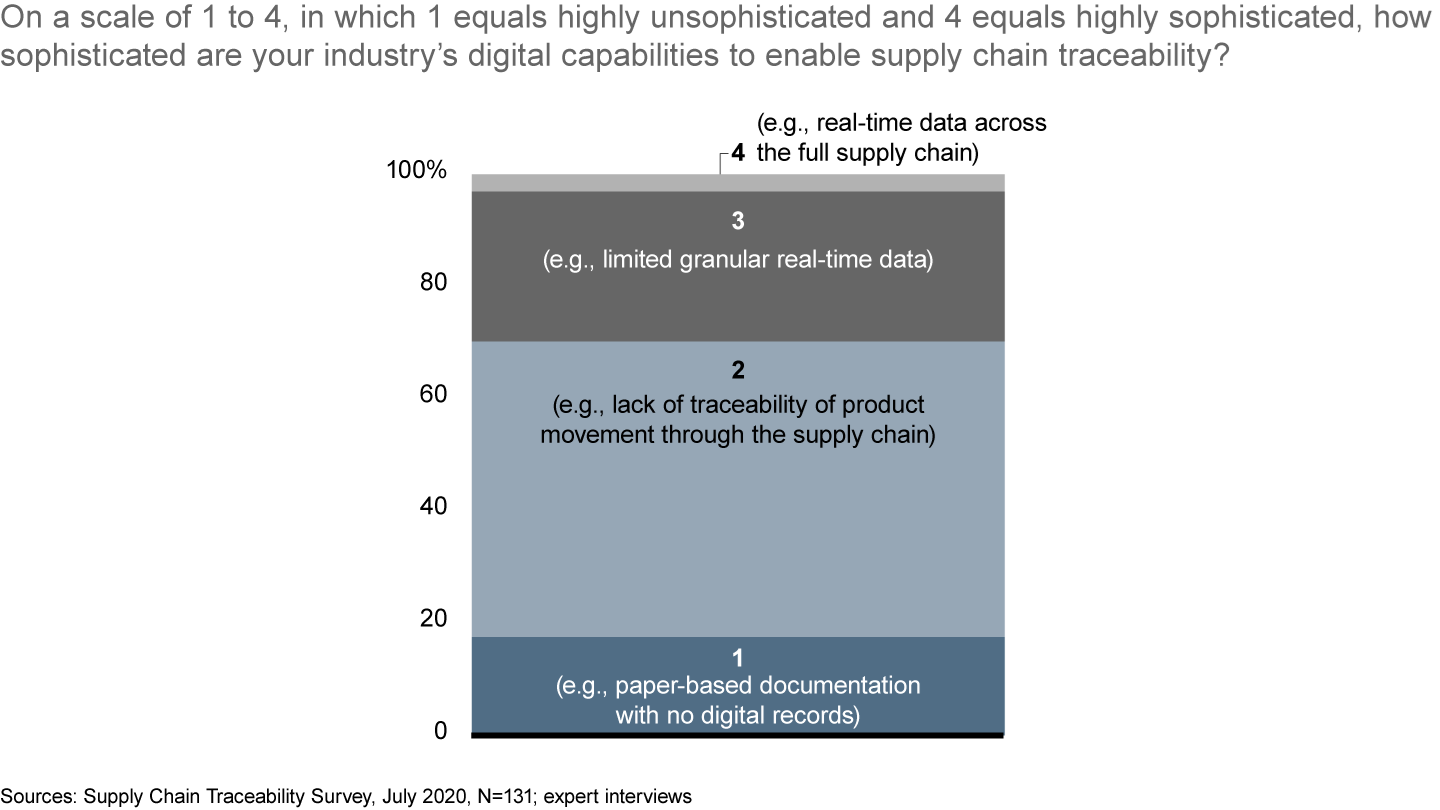
Unreliable or nonstandard data is the leading barrier to achieving traceability
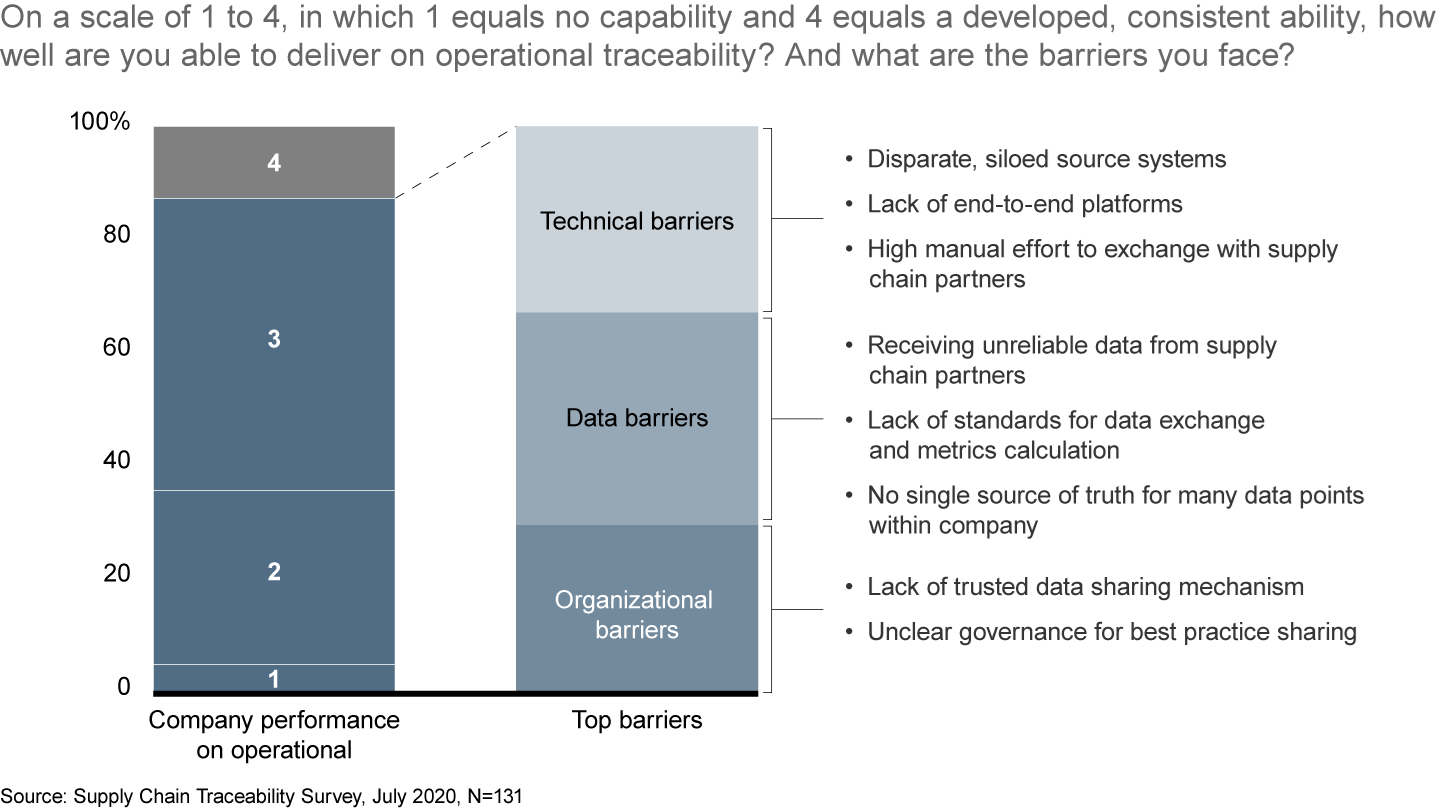
Carefully define how visibility and traceability will provide value to your company. To produce the greatest benefits, companies should pursue visibility and traceability approaches that are closely tied to their business and customer strategy. Walmart, for example, reduced the time required to trace the provenance of mangoes sold in US stores by more than 99% by using IBM’s Hyperledger Fabric platform. Honeywell’s GoDirect Trade platform digitizes provenance and quality tracking, enabling users to reduce the total time required to resell aircraft components by 50%. Maersk’s TradeLens achieved a 40% reduction in transit time for shipments by digitizing the handshake process among shippers, regulators and recipients.
Map out the data model, and begin collecting the necessary data across the supply chain. Start by asking the following questions:
- Which data do we need?
- Where is it captured?
- How trustworthy is it?
Despite vast amounts of siloed, partially structured data, companies often still find that the data they need doesn’t exist in internal systems—or it isn’t available at all. They must learn how to integrate external data sources, including logistics systems and suppliers’ enterprise resource planning (ERP) solutions, and how to begin collecting critical data that isn’t available today. A good data model also clearly describes the relationship between data elements, and it ensures that the right business events and information will be captured to support business analysis.
Assemble a next-generation technology stack to facilitate data collection, analysis and sharing. Most companies lack a platform specifically designed to provide visibility and traceability across the supply chain. Instead, they typically try to combine legacy ERP solutions with homegrown visualization and analysis. But these systems weren’t built for that purpose, and their ability to automate traceability and visibility with multiple ecosystem partners is limited. At the same time, making a big new technology investment in this rapidly evolving space carries risks of its own, with technology providers entering the supply chain market with solutions from many different angles.
- Information led: Some solutions center on providing aggregated industry information, benchmarks and market intelligence to empower decision making.
- Certification led: Other solutions provide environmental, social and governance ratings based on shared information.
- Software led: Yet another set of solutions employ use cases and information sharing as enablers (for example, data analytics engines or cloud storage solutions), point solutions focused on one set of supply chain priorities, or end-to-end supply chain engines.
- Service led: Consulting services provide strategic advice that builds on the insights delivered by software or data aggregation solutions.
Adding to the complexity, companies face a mix of for-profit and not-for-profit players that offer a wide range of solutions focusing on everything from visibility to strategy. In the end, a compelling ecosystem will likely include elements from each of these various solution types. When evaluating the market, companies should consider how these new systems will fit into their current systems landscape. Some systems will primarily serve as sources for required data, while others will be the enablers for aggregation, analysis and sharing.
Implement the appropriate data operating model both inside and outside the company. Full supply chain traceability and visibility depends on data sharing, but most companies have found that is hard—and not for technical reasons. Companies often find that the data they receive isn’t valuable or trustworthy or that sharing collapses because of privacy concerns or because there was no trusted party coordinating the effort (see Figure 6).
Privacy concerns and untrustworthy data make companies reluctant to share their own data in exchange for access to aggregated industry data
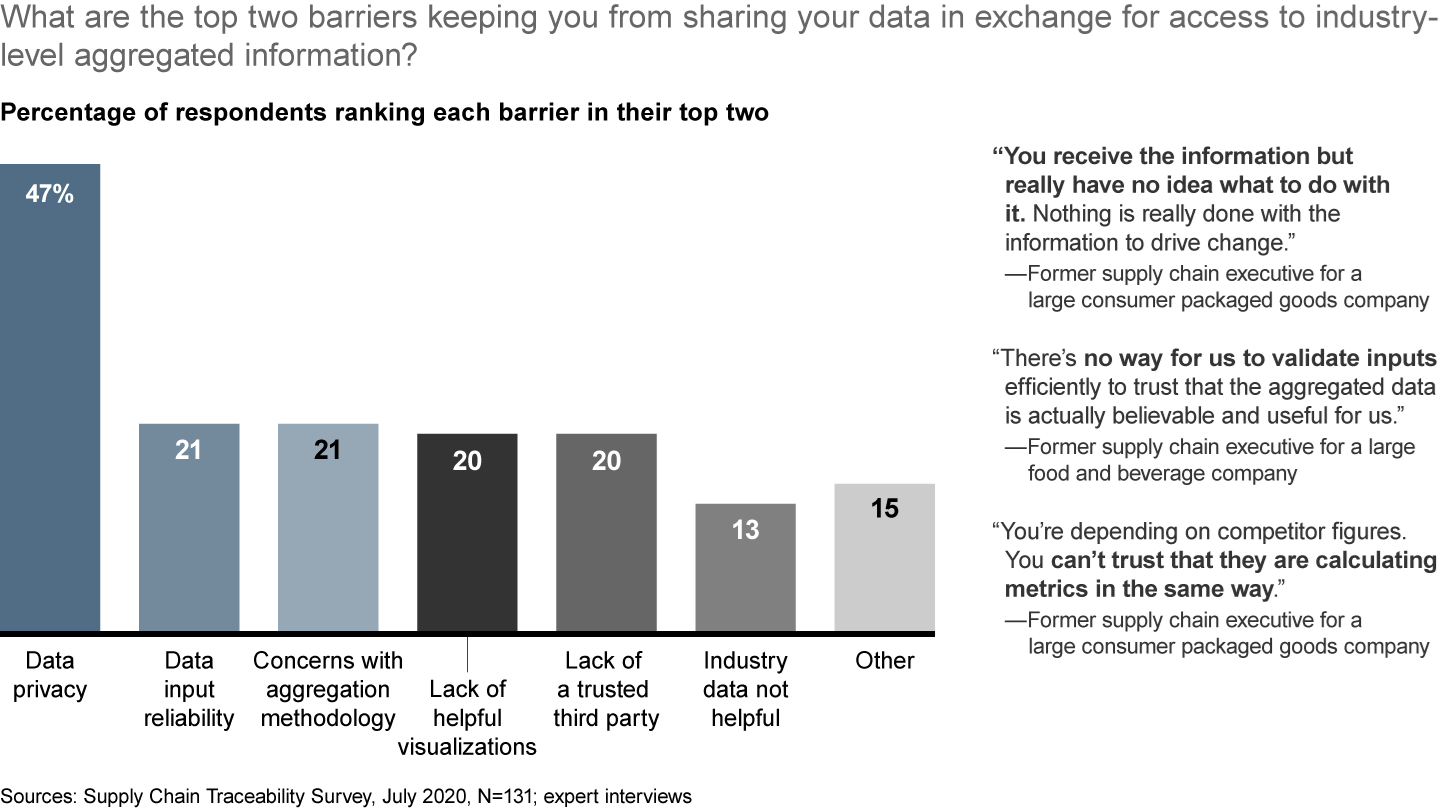
Effective data sharing starts inside each company by overcoming silos to create a single source of truth for relevant data. They need processes, systems and talent for data collection and cleansing, and they need analysis to turn data into insights that can fuel business decisions. Only then can they figure out the appropriate way to share the data with ecosystem partners. That, in turn, will present new questions about the level of data aggregation, the sharing frequency and life span of the data. Companies also need to consider who owns the shared data and the resulting analyses, and they need to figure out how to ensure strict privacy for the source data.
Multistakeholder collaboration as accelerator
No company can build visibility and traceability into its supply chain on its own. Instead, the effort requires collaboration among multiple stakeholders within a sector to set standards and fund platform-type investments, to focus resources and share costs, and to gain traction. If multiple players in a sector align on a common language, standards or data model, all will benefit from accelerated capability development, less decision complexity, easier benchmarking and collaboration.
There is precedent for this sort of effort: The creation of generally accepted accounting principles allowed companies to report common financial metrics and gave investors and other stakeholders a way to reliably benchmark financial performance. Similarly, the automotive industry agreed more than 40 years ago to use an electronic data interchange as the standard for planning and delivery schedules to support lean manufacturing and just-in-time delivery.
In recent years, several sectors have combined forces to accelerate traceability and visibility. For example:
- IBM’s Food Trust, founded in 2017, addresses the need for smarter, safer and more sustainable food supply systems by connecting an ecosystem of producers, suppliers, manufacturers, retailers and other stakeholders. The blockchain-powered solution helps ecosystem participants eliminate supply chain bottlenecks, enhance their reputation for quality, ensure safety and regulatory compliance, and build a sustainable supply chain with less waste and spoilage.
- The MediLedger Project, launched in 2017, brings together pharmaceutical manufacturers and wholesalers in a working group to explore the potential of blockchain to meet the Drug Supply Chain Security Act requirements for a track-and-trace system for US drugs. The project became the MediLedger Network, a fully decentralized network that aims to inspire industry players to develop multiple solutions based on current business issues.
The key questions to address
Despite the challenges of building such networks, many industry leaders agree that in the future, companies will share data across a supply chain as well as their sector and that they will work together to improve the supporting technology and analytical engines to ensure efficient, reliable, resilient and sustainable supply chains.
If that is the future, how do we get there? Our view is that industry leaders (moving ahead of regulators) will likely push the initial development of the platforms and set the standards, after which they’ll be joined by other industry players who see the value. In order to gain industry-wide traction, industry leaders need to run pilots that set a standard for multistakeholder collaboration among suppliers, customers, tech providers and other players. Lessons learned from these pilots will form a foundation on which to build future versions of the platform and help define how to scale it across the industry. In the past, efforts to define the full initiative up front and then roll it out on day one foundered; this approach may look fantastic on paper, but it doesn’t work in reality. The cost of aligning too many stakeholders gets in the way of solving an already complex, multidimensional problem. An Agile approach that starts small and gains traction with compelling business results is more likely to lead to alignment around standards and certifications that can then be scaled up across use cases and participants.
Below, we look at the key questions industry leaders need to answer in order to develop visibility and traceability platforms and practices (see Figure 7).
An industry-wide visibility and traceability solution requires four key ingredients
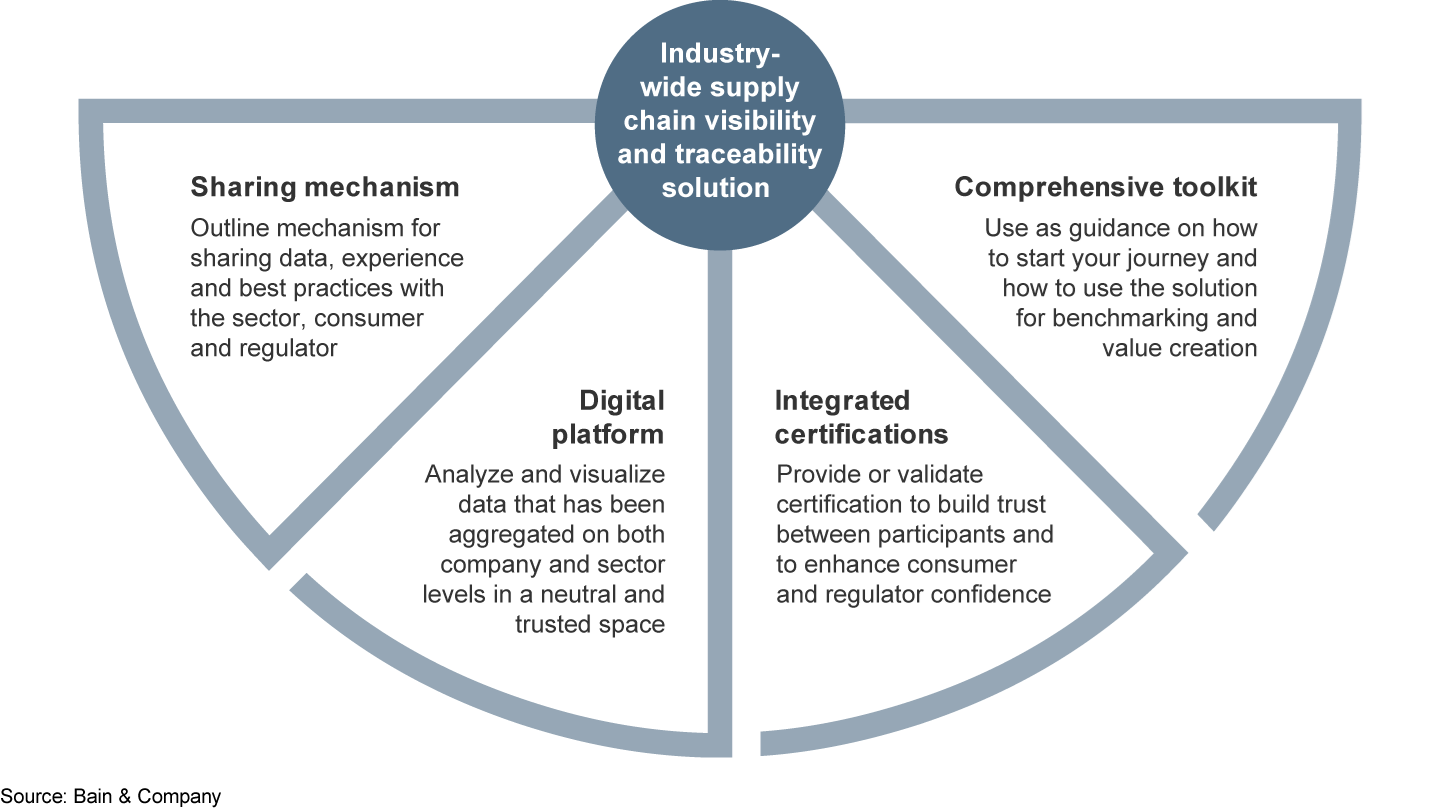
How do we create an environment that fosters sharing? Companies will need to work with partner organizations and even their competitors to achieve true visibility and traceability across supply chains. Because reluctance to share supply chain data with competitors remains very high—only 6% of executives who responded to the World Economic Forum/Bain survey feel comfortable with this today—these efforts also are likely to require the involvement of trusted neutral entities, such as industry associations, to truly achieve sector-wide adoption. Two-thirds of executives told us that they are comfortable sharing operational data with industry associations (see Figure 8).
Few executives are willing to share data with competitors, but most are willing to share with industry associations
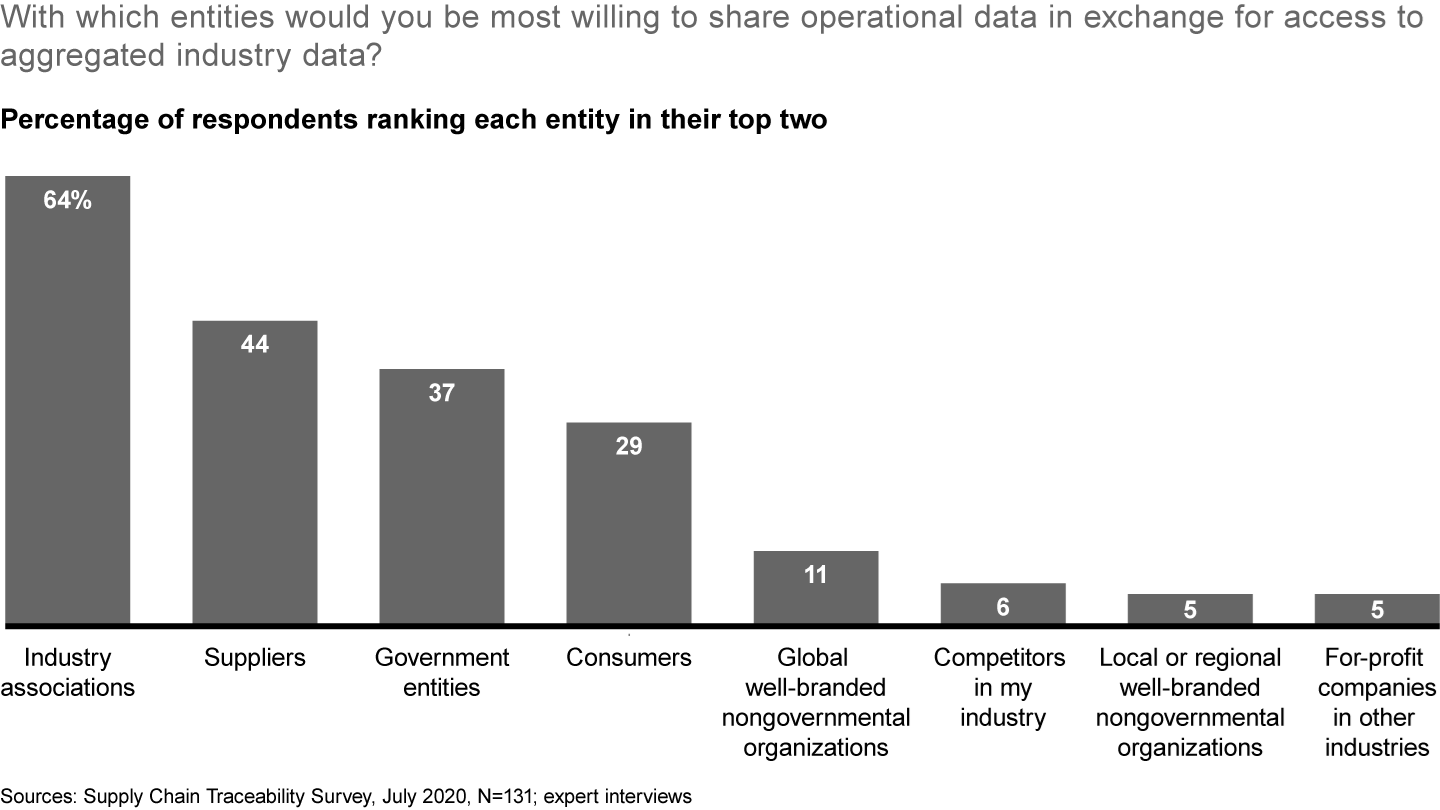
Sharing is not limited to data. Not-for-profit organizations, including industry associations, are critical to encourage the sharing of experience and best practices. These organizations can rally stakeholders together and ensure that industry standards and exchange mechanisms serve all industry players. For example, GS1, a not-for-profit organization, helps everyone involved in making, moving and trading goods to automate and standardize their supply chain processes, using the common language of GS1 global standards. GS1’s standard library includes the GTIN (global trade item number) standard, which provides different globally recognized ways to add an identifier such as a barcode to a product.
Fostering sharing requires a common language as a foundation; it also requires a strong operating model that clarifies sharing mechanisms. That model needs to be flexible enough to scale from a pilot setting to a sector-wide solution, and it is essential to ensure fair representation of multiple stakeholders in decision making as well as to clarify how to cover the ongoing costs of operating and scaling the solution. Additionally, it’s important that all participants receive attractive incentives—the strongest incentives will be those that directly lead to improved sustainability, efficiency, resilience or reliability of participants’ supply chains.
How do we bring the digital platform to life? Multistakeholder collaboration across an industry will depend on a digital platform that offers safe data and best practice sharing. Given the rapid pace of innovation in the supply chain visibility and traceability solutions market, it’s likely that a technology company will need to shoulder the ongoing hosting and development of the platform and then commercialize the solution after the value has proved robust in pilots. The digital platform should be able to sit on top of existing company-specific supply chain and analytics solutions and integrate with them as needed, allowing users to visualize key information and to enable decision support.
How do we create trust and confidence in certification? Certifications play a key role in building trust between companies and consumers and among companies within a supply chain. Working with the digital platform, certification providers can certify the inputs and processes of each platform participant, certify the digital platform itself, or certify the analytical results that it produces. Certifications that can be used for communications and marketing offer additional incentives for companies to participate. This is no doubt easier said than done; certifications have existed for decades and continue to struggle not just with acquiring accurate data but also with producing real change on the ground. But improving one will help improve the other—that is, if traceability solution providers collaborate with certification providers.
How do we mobilize and create value? Creating end-to-end supply chain visibility and traceability through a multistakeholder collaboration is a challenging task and requires significant investment from every participant. To avoid getting lost in the details or spread too thinly, we believe that every company involved needs to develop a toolkit to guide their in-house and collaborative visibility and traceability efforts. The toolkit should include a playbook for how to build the required capabilities in terms of people, systems and processes; guidance around how to benchmark performance, progress and development against sector; and clear roles and responsibilities for deriving business value and sustainability from the newly available insights.
Companies looking to get started should recognize that they no longer have to think of efficiency, reliability, resilience and sustainability as inevitable trade-offs. As supply chains become more transparent and provide more data about each of these elements, an increasingly holistic view should allow executives to improve their design even further, resulting in fewer trade-offs and offering opportunities for these elements to complement, rather than conflict with, each other.
Creating a new, balanced supply chain requires a two-track approach. Inside your company, you should accept the uncertainty that comes with innovation and approach the challenge both present-forward and future-back. That means pursuing two to three opportunities that solve key challenges for your organization today so that you can realize immediate value and learn from each opportunity. At the same time, think hard about the future. What would your ideal supply chain and supply chain capabilities look like 10 years from now? Adopt a clear future vision, and then work backward to determine which capabilities you will need to build to win.
And outside your company, get engaged. Look for the organizations within your sector (and beyond) that are wrestling with these same issues and actively trying to solve them. This is not a business problem that can be solved by one company alone. The companies that take the lead in collaboration today will have the advantage. Those that sit on the sidelines will have to be content with whatever the industry ultimately adopts. But those that seize the opportunity now will set the standards, both within their industry and across sectors.