Brief
At a Glance
- Automakers are looking for ways to reduce emissions and the use of new materials, while meeting a growing population’s demand for mobility.
- Beyond sustainability, circularity should help generate new value for the industry, for example, by reducing the costs and risks of accessing virgin materials.
- Becoming more circular will require automakers to develop new capabilities, such as incorporating reused, recycled, and remanufactured components.
- Automakers and others in the industry must also pursue new partnerships and investments, to ensure long-term access to competitively priced supplies.
Automakers around the world are looking for ways to increase circularity in order to reduce waste and Scope 3 emissions, strengthen supply chain resilience, and generate new value as they transition to a low-carbon future. Many automakers have committed to programs to enhance circularity, including using more recycled materials and remanufactured components in production, and better managing the reclamation of materials from vehicles at the end of their useful lives.
In the mobility sector, circularity means more than just recycling the parts from scrap vehicles. Full circularity includes adhering to principles of circular design (for example, reducing the need for materials, cutting waste, and increasing the potential for end-of-life reuse and recycling), increasing the amount of recycled content in production, and deploying business models that improve vehicle utilization—meaning, they are used more hours of the day. Because mobility represents a significant share of global emissions (about 30%), any comprehensive approach to mitigating climate change must substantially reshape the ways that vehicles are produced, used, and recycled. The sector is responsible for about 10% of the world’s material footprint, so circularity is also key to decoupling the need for transportation from material consumption.
Europe’s automakers are leaders in circularity, with a total circularity rate of 40% (calculated as the weighted average of the percentage of circular material inflows and outflows), driven in part by strong regulation. (Bain uses the Circular Transition Indicators methodology, as developed by the World Business Council on Sustainable Development.) While EU policy initially focused on vehicles at the end of their useful lives and battery recycling, it now extends to the design phase with recycled content mandates and considers the recyclability of the full vehicle. These policies will continue to evolve over the coming decade, creating a strategic opportunity for companies that navigate the transition early. Because of this lead, the entire global sector can learn by looking at what Europe has accomplished and where progress can be made in the years ahead.
In 2019, the global economy consumed more than 100 billion tons of resources—primarily virgin metal ores, fossil fuels, biomass and minerals—and only 8.6% of this was cycled back into use.
Mobility is a fundamental need and will fuel the demand for cars and trucks for decades to come. Yet the industry faces severe challenges responding to this demand if it takes a business-as-usual approach. Recent supply chain disruptions have emphasized its vulnerability. For example, semiconductor shortages have hurt auto sales across regions. (For more, read the Bain Brief “A Chip Shortage Recovery Guide.”) Competition for virgin materials and rising insecurity in the supply of critical components compels automakers to develop other sourcing strategies, including recycling, reusing, and remanufacturing components.
Circularity is more than a series of measures to reduce waste and emissions. It is also a lens that companies are applying to their businesses to spur innovation and assess potential disruption. Such an approach can illuminate significant shifts in profitability across the value chain and provide a means to ensure resilience in supply so that automakers can continue to produce the vehicles that the global economy demands.
Reuse and recycling in the vehicle life cycle
The European Union is a front runner in terms of regulatory development in circularity, and that has spurred Europe’s automakers to move assertively to organize their efforts in response to and ahead of potential policy developments.
The recycling rates published by the European auto industry are high: an estimated 89% of end-of-life material is collected and sent to recyclers, with aluminium and steel comprising the largest portion of secondary materials. However, when recycling losses and inefficiencies are considered, the percentage drops to 78%, falling further to 59% when the number of end-of-life vehicles exported from Europe are considered. Recycling rates for key materials such as nickel, cobalt, manganese, and lithium are also low, and the growth of battery electric vehicles (EVs) creates an urgent need to improve recovery levels of these materials.
New car production in Europe uses about 23% recycled materials, and that could rise to 59% by 2040—a massive boost to the industry’s circularity (see Figure 1). Ensuring a secure supply of recycled content will be key. As collection techniques and the recycling supply chain improve, design engineers will be able to use more recycled materials in new vehicles, including steel, aluminium, lithium, and plastics.
With strong adoption of circular principles, Europe’s passenger vehicle sector could go from 40% circular today to 66% circular by 2040.
While the electrification of cars and trucks can reduce emissions over their lifetime, the emissions are higher during production due to the carbon intensity of mining battery metals. Electrification also makes vehicles heavier, due to weight of the batteries. Because of this, optimizing design for material efficiency and for higher levels of low-carbon and recycled content becomes even more important.
The EU is raising the bar on recycling of battery materials. Used-car batteries must be tested first for refurbishment, remanufacturing, and second-life potential before recycling becomes an option. When batteries are recycled, the rules mandate high levels of material recovery—for example, 70% of lithium and 95% of cobalt, copper, and nickel by 2030. The new rules also up the ante on carbon accounting, requiring that the battery’s carbon footprint and other details be tracked over its life cycle. Some companies are already moving on the inherent opportunities. Swedish battery developer Northvolt (which is about 20% owned by VW) produces battery cells with recycled nickel, manganese, and cobalt recovered from battery waste. The company has more than $55 billion in contracts with customers that include Polestar and Volvo. Mercedes-Benz is also building a battery recycling plant in Germany, using the recovered materials to make more electric vehicles.
By 2050, private cars could account for only 40% of urban transport miles worldwide, down from 67% today. Shared and public mobility will make up a larger share of the total, increasing overall utilization of vehicles. Shared vehicles are the fastest-growing mode of transport, and mobility services will account for an expanding share of the global profits in the industry.
There is also potential in using recycled materials and components in repairs. In 2020, only 2% of the parts used for auto repairs in Europe were recycled; raising that to 12% by 2040 could reduce emissions and increase profit margins (see Figure 2). Refurbishing an existing engine requires only about 15% of the emissions that it takes to make a new one.
Five strategies help reduce auto industry greenhouse gas emissions from production by 60%
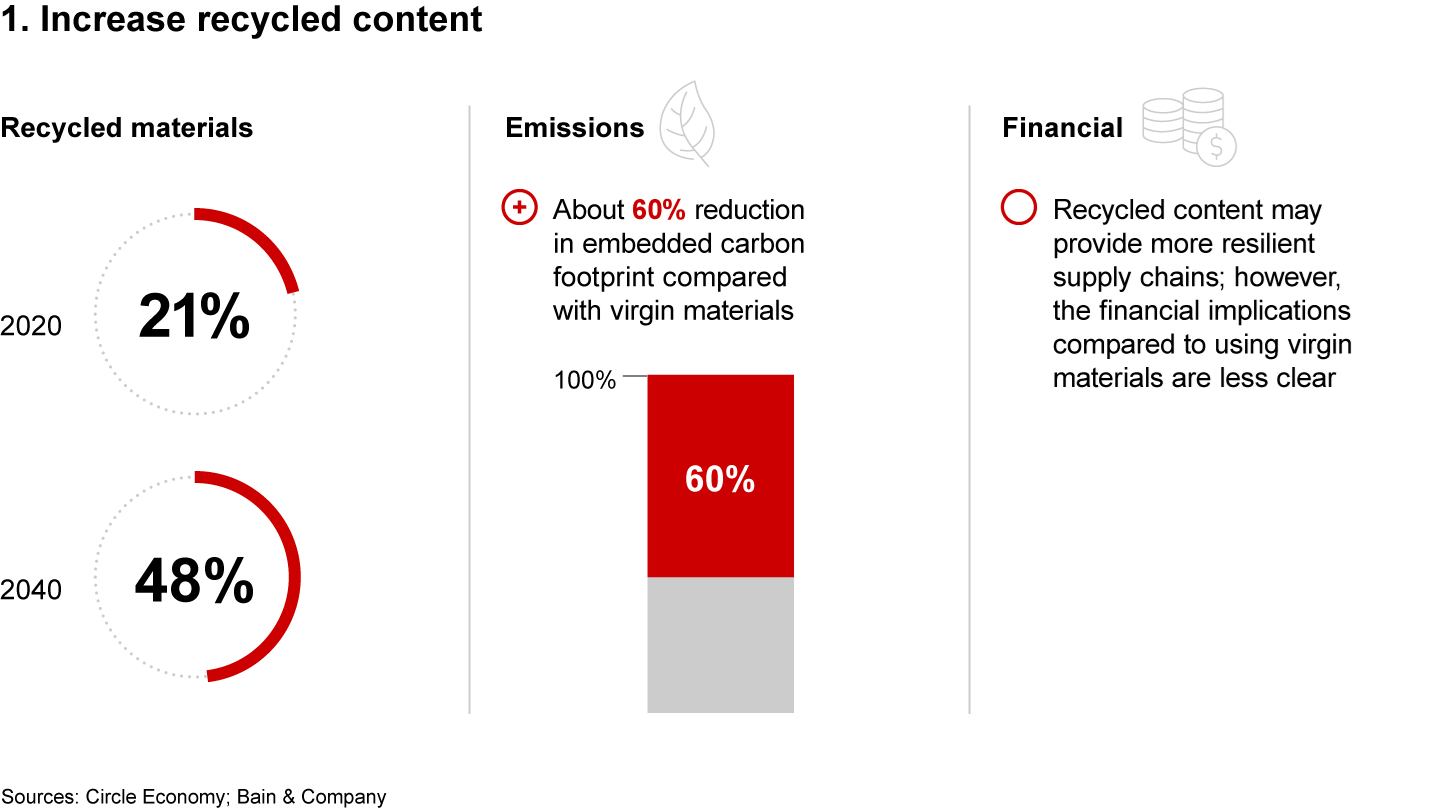
Five strategies help reduce auto industry greenhouse gas emissions from production by 60%
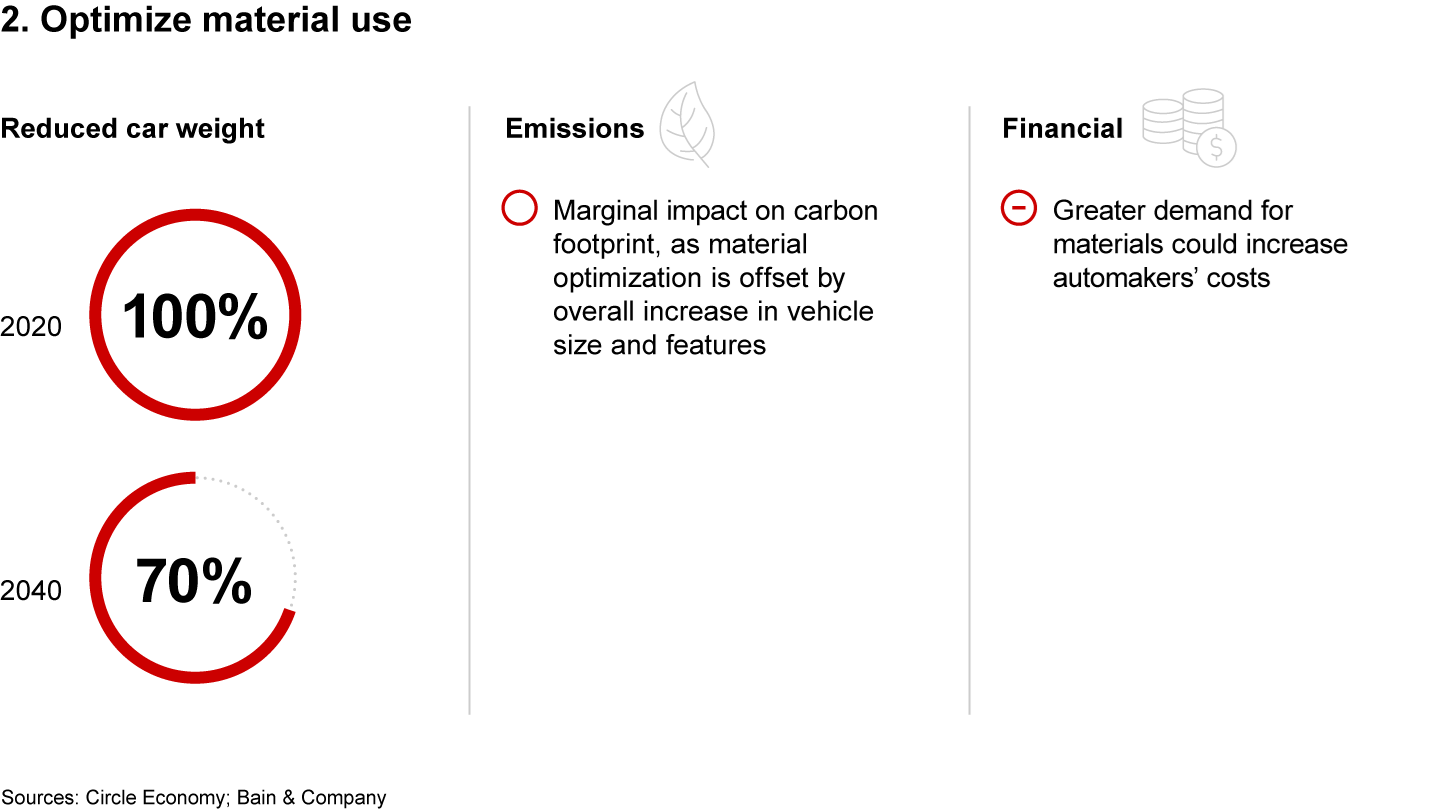
Five strategies help reduce auto industry greenhouse gas emissions from production by 60%
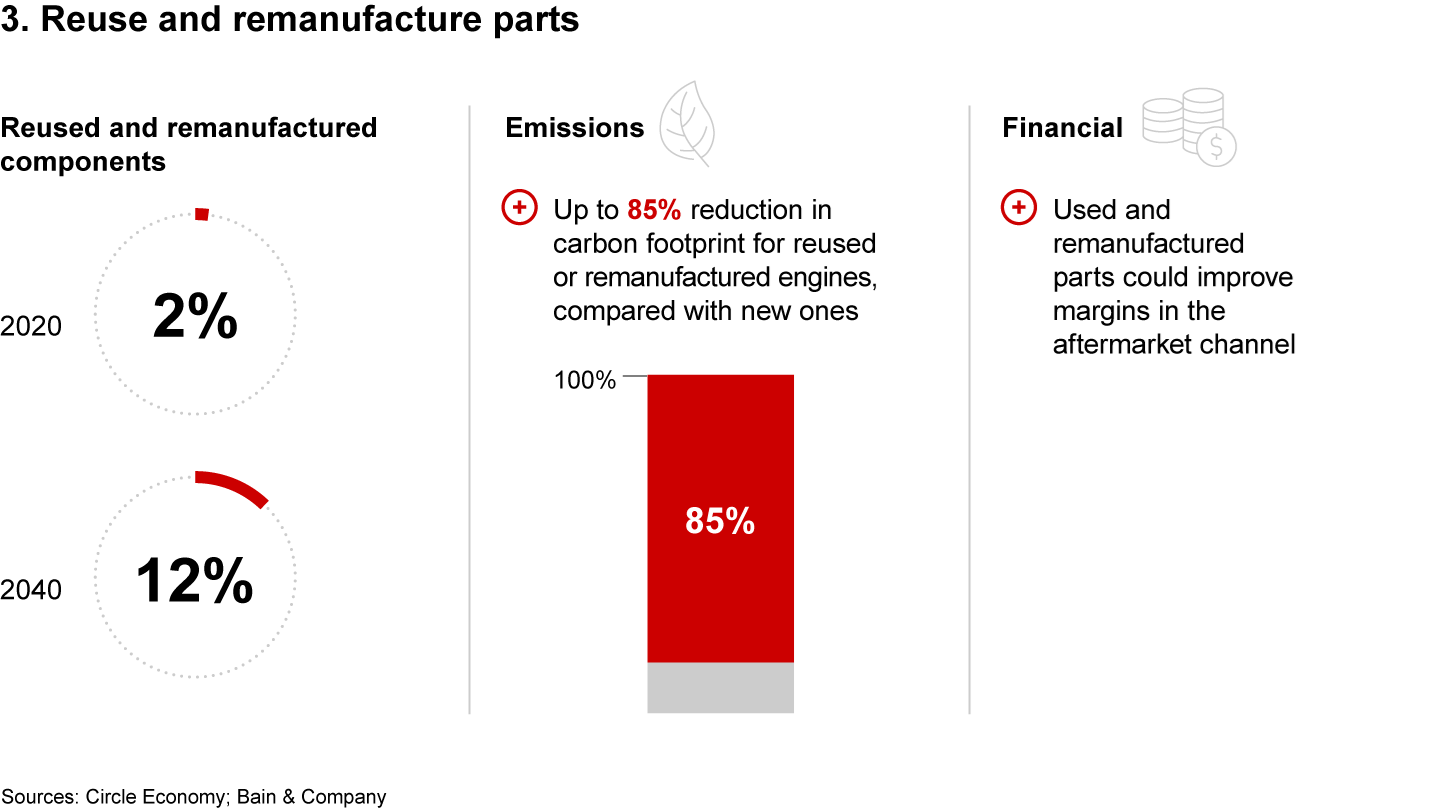
Five strategies help reduce auto industry greenhouse gas emissions from production by 60%
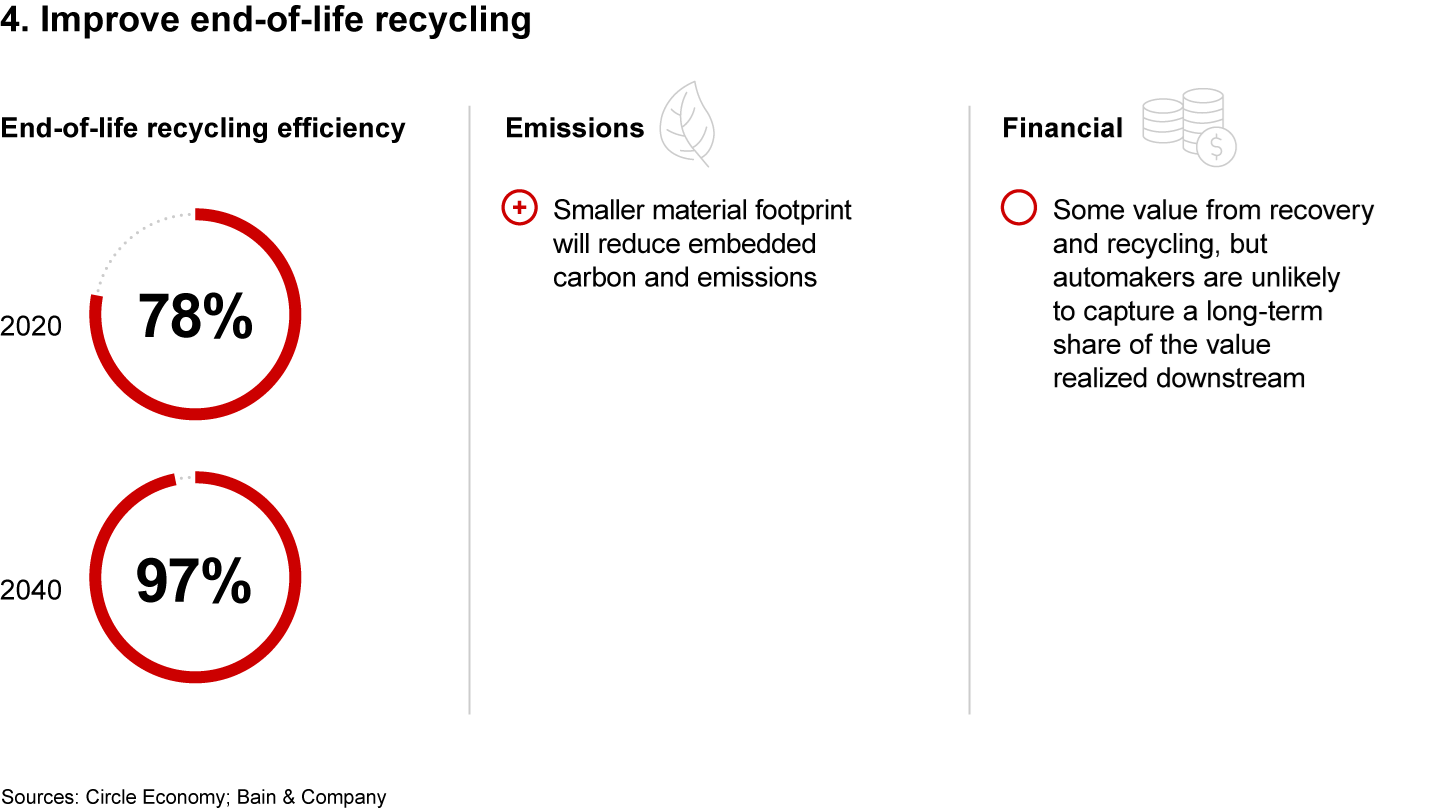
Five strategies help reduce auto industry greenhouse gas emissions from production by 60%
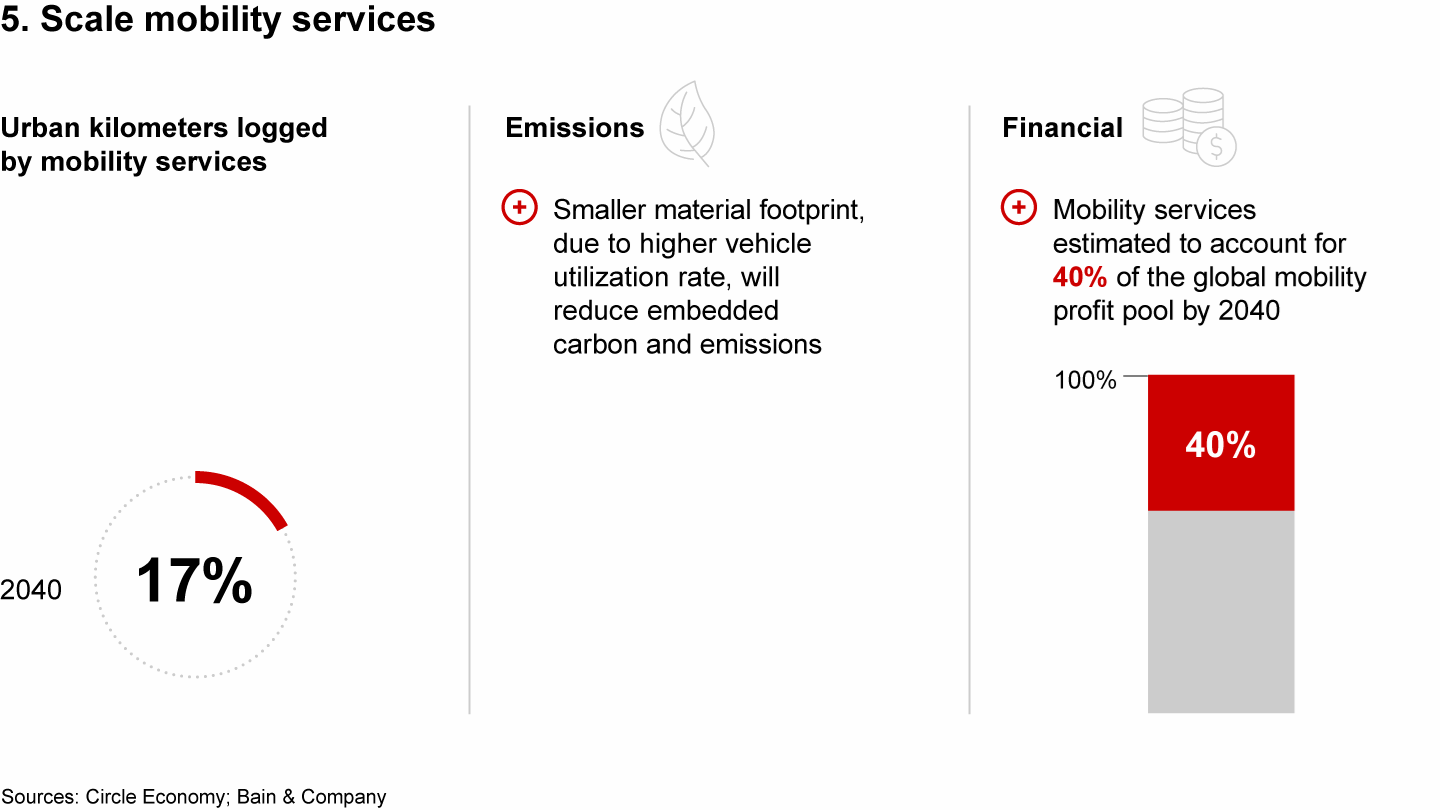
End-of-life processing and material separation techniques are already developing, partly because of government policies, to maximize the value extracted from old cars and trucks. By 2040, nearly all the metals used in EV batteries could be recycled, along with most of the glass and up to half of the textiles in the vehicle. Recycling efficiency could rise to 97% by 2040, up from 78% today. Increased circularity will be essential for reducing the industry’s embodied carbon footprint.
Improving the industry’s circularity
As automakers grapple with a range of disruptions to their core business, including shared mobility, autonomous driving, and electric power trains, circularity strategies can complement these efforts, providing new avenues for profitable and sustainable growth. Automakers can take several actions now to lead the circular transition.
Harness circular strategies to reach net-zero goals. Circular strategies can cut greenhouse gas (GHG) emissions embodied in materials and are therefore vital to achieving net-zero goals—which cannot be realized through electrification of the vehicle fleet alone. Adopting strategies such as including recycled content, optimizing material use, and improving recycling efficiency can help companies move toward net zero. Reducing emissions also reduces exposure to current and future carbon taxes, and circular strategies such as reuse and remanufacturing can create new value and growth on their own.
Make circularity the new normal across business models. Most cars are privately owned by one person or family, and they sit unused up to 95% of the time. Mobility services and the advent of robocabs (commercially at scale in the 2030s) should drastically increase utilization. Under some scenarios, the rise of self-driving vehicles could significantly reduce private ownership of cars in some urban areas.
Automakers are responding to this threat by exploring opportunities in mobility services. Renault, for example, has committed to increasing the use-rate of vehicles by at least 20% with new mobility service models, and other automakers have experimented with mobility services. We may also see new entrants pursuing potentially profitable areas of the future market. Reuse and remanufacturing for robocabs, in particular, will further increase circularity and boost profitability, which should interest operators focused on total cost of ownership. More fleets of shared vehicles will create a reliable customer base for used and remanufactured parts.
Secure long-term and cost-competitive access to recycled materials. Greater demand for circular inputs will require companies to reflect on how they can secure long-term, competitively priced supplies. Investments and partnerships within end-of-life material recovery and recycling can help companies be less dependent on a volatile and limited market of good-quality secondary materials. Volvo, for example, has invested with battery maker Northvolt to ensure access to a more secure battery supply as it electrifies its fleet.
What pioneers are getting right
In our experience, leaders who are pioneering the transition to circular business strategy do three things well. They map the potential for circular flows in their existing value chain, identify the best opportunities, and start scaling a circular business and ecosystem.
Scan the value chain for ways to improve circular flows. While Figure 1 shows the materials used for production, maintenance, use, and disposal at the sector level, the picture looks different for each company. Mapping a company’s material flows helps leaders identify resource use and waste in their own value chain and find ways to improve circular flows that create new value, such as using more remanufactured vehicle components.
Look ahead to predict disruptions and find new opportunities. As companies better understand the costs and benefits of circularity, they can anticipate possible disruptions and new business opportunities. A deeper familiarity with the entire value chain can help identify control points, such as direct-to-consumer vehicle subscriptions or mobility service offerings including robocabs and ride-hailing services.
One automaker set out to understand what the material flows for its value chain would look like in a circular economy, examining materials sourcing, component manufacture and production, vehicle use, and end-of-life options. Although the team didn’t have full transparency into its upstream supply chain, the exercise delivered powerful insights. The company identified several attractive opportunities to reduce resource consumption, including one involving the remanufacture and reuse of parts and components. Another focused on cutting emissions by using more recycled content, while a third sought to capture value from end-of-life processing of batteries, reducing material costs.
Scale the ecosystem for success. No company can solve circularity on its own, so it’s essential to understand where to collaborate and where to compete. Industry standards and coalitions are forming, such as the Global Battery Alliance, a group of more than 120 public and private organizations working to establish a sustainable battery value chain. When building (or buying) circular solutions, leaders are doing this on scalable platforms that suppliers and other external partners can use. Traceability platforms, for instance, can enable circularity by creating transparent material flows in real time throughout the product life cycle. Transparency requires a systems and data infrastructure that can seamlessly connect ecosystem members and data sources.
Improving circularity offers a route for automakers to provide customers with the mobility and convenience they need, in a more sustainable way. There are real opportunities for the industry, including savings and security of supply. But to make the most of these gains, executives need to think holistically, across every element of their operations and supply chain. Although the journey will take decades, leaders should take an assertive approach and get started today.