Report
Executive Summary
- Large construction projects frequently run over budget and beyond schedule. That’s got to change. To pay for the energy transition, companies need to spend capital more efficiently.
- Deploying cross-functional teams and Agile methodologies in the engineering phase of projects can save time and money.
- More transparent procurement processes, with cost benchmarks, can increase the efficiency of money going to suppliers.
- Better cooperation between construction contractors and managers can improve efficiency in construction; one mining company recovered 12 months of lost time and saved over $500 million on a major project.
This article is part of Bain's 2021 Energy and Natural Resources Report.
No sector spends more of its revenues on capital expenses than the companies in energy and natural resources (see Figure 1). They’ll have to spend much more as they retrofit old assets and build new ones that meet increasingly strict sustainability requirements, those imposed on them by regulators and the goals they set themselves. Estimated spending on infrastructure to meet the needs of a decarbonizing economy range as high as $50 trillion over the next three decades.
Some of these capital projects represent new opportunities where incumbents lack experience―for example, in hydrogen, renewables, carbon capture and storage, and rare earth materials. These will carry new risks, and that will make it even more challenging for these companies to properly allocate capital to these investments.
Energy and natural resources industries spend a greater share of revenues on capex than other industries
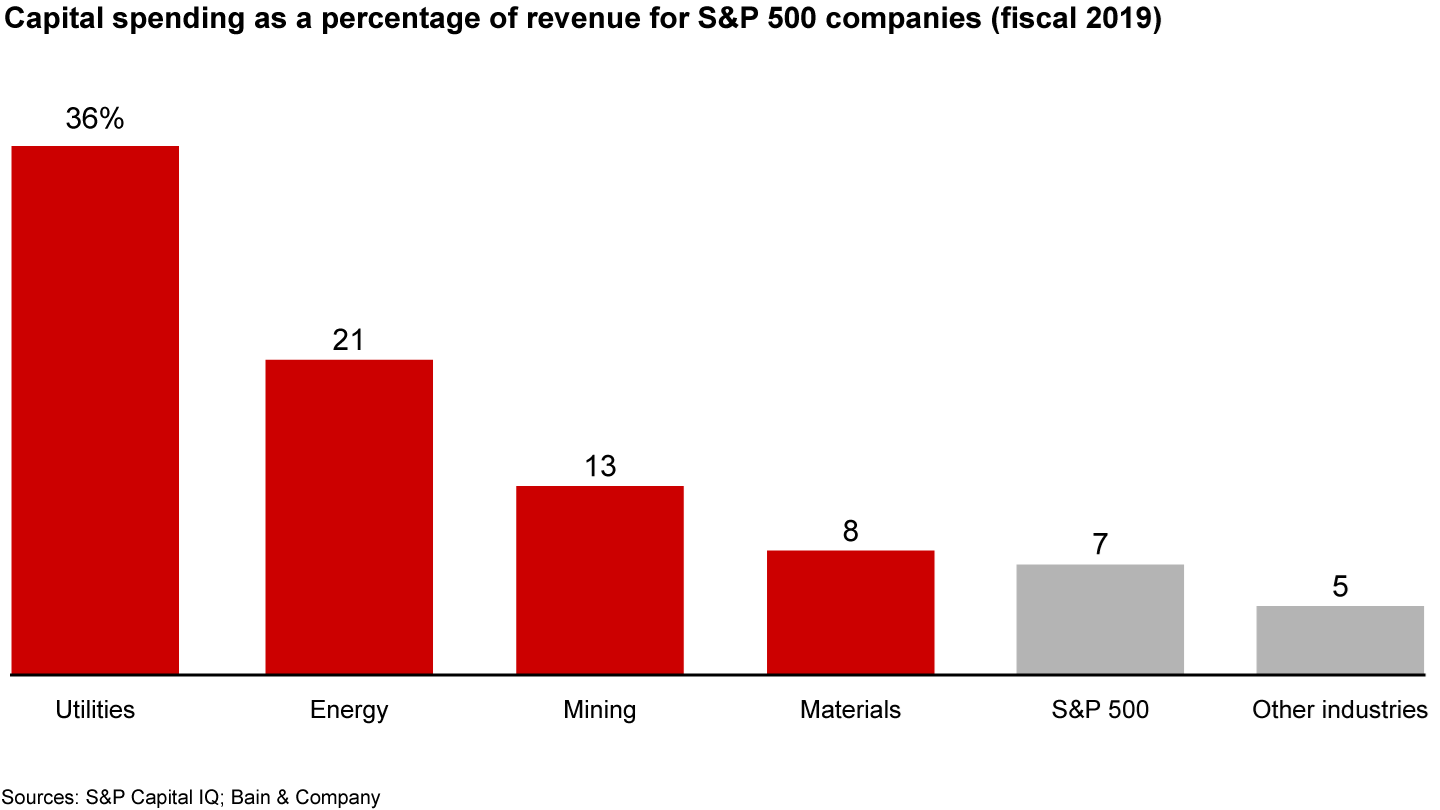
But capital projects across the sector are already notorious for delays and cost overruns (see Figure 2). Bain’s analysis of 76 large energy and natural resources projects around the world found that 34% of them incurred cost overruns, which averaged about 17%, and 84% faced delays, which averaged more than two years. Those that do finish on time often have budgets that allow for low productivity and high costs. Many of these are megaprojects in oil and gas, utilities, chemicals, and mining, netting out in the billions and tens of billions of dollars. The vast scale of these projects, their complexity, and the long timelines all contribute to the many delays and overruns. As the development requirements become more stringent to meet environmental and community demands, these projects will become even more expensive and complex. For example, some mines are using ocean water so that their operations don’t drain the fresh groundwater supply. But using ocean water―transporting and desalinating it―can add 15% to 30% to a multibillion-dollar mining project. Implementing carbon-capture or emissions-reduction technologies on industrial plants also increase the costs.
Many energy projects encounter delays and go over budget, leaving significant money on the table
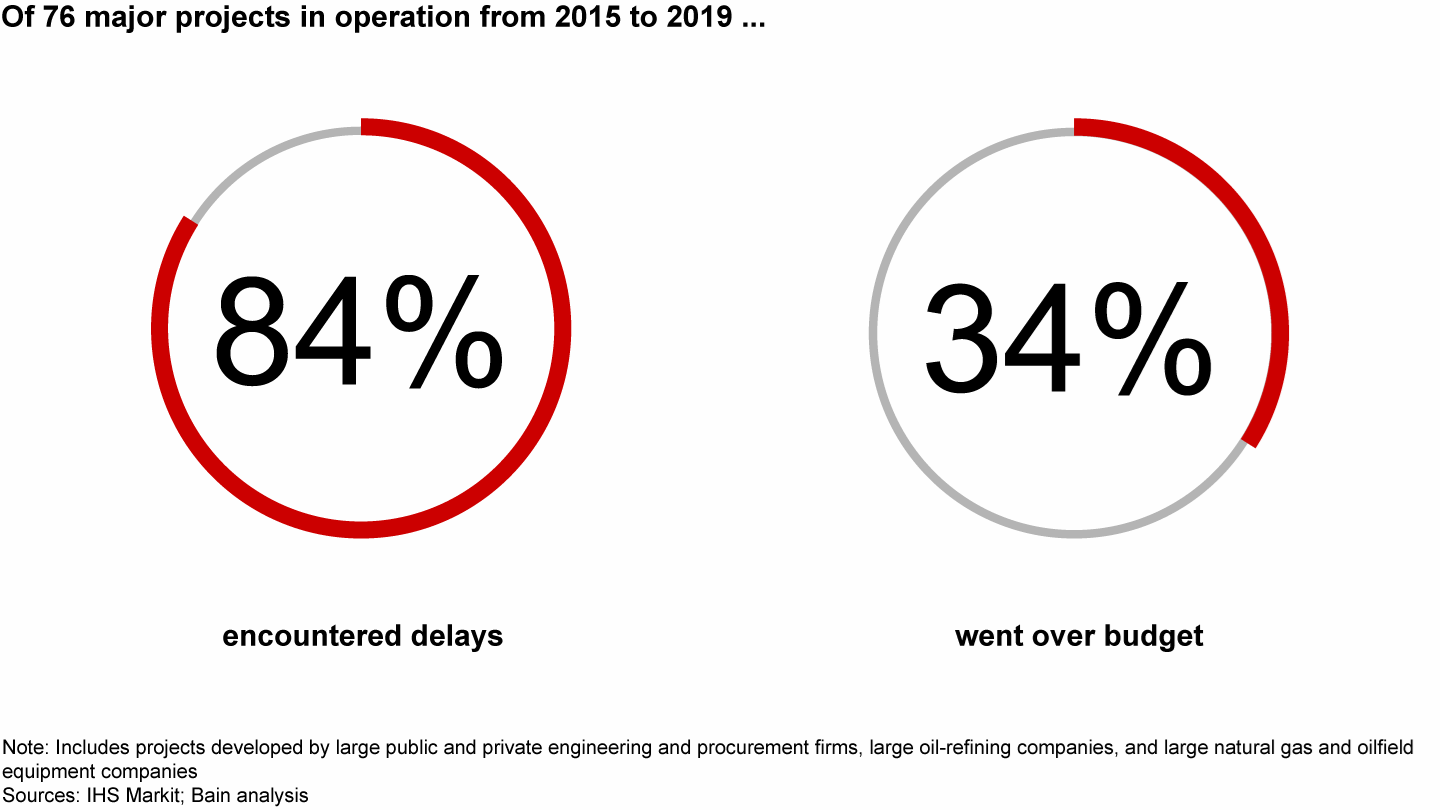
These companies really need to develop and build new capital projects more efficiently if they want to remain leaders. Oil and gas companies, utilities, and chemicals and mining firms will compete for capital and other resources as they seek out first-mover advantages, trying to position themselves higher on the learning curve than competitors that take a wait-and-see attitude. Slow movers may find themselves saddled with stranded assets and businesses in decline if they can’t adapt to new demands. Given all that’s at stake, capital efficiency advantages of even 10% to 20% or shorter schedules to get projects to market could have existential implications.
To try to capture those gains, companies are redesigning their models for engineering, procurement, and construction. One of the most important steps is adopting an Agile methodology with a lean mindset shared by the project team, the engineering contractor, the sponsor, and the client. In procurement, better analysis of costs and greater transparency are helping to rein in costs. And in construction, closer cooperation among the construction contractors and construction managers, coupled with a “red is good” mentality―that is, a willingness to deal with problems rather than ignore them―can improve capital efficiency. Companies that are executing well on these three dimensions are reducing capex by 15% to 30% and shortening construction schedules by 6 to 18 months.
More Agile engineering
For a long time, the engineering phase of capital projects has been trapped in a single way of working that results in long development times and frequent rework. Firms usually outsource the design task to the engineering firm with the lowest bid and limit their own involvement to reviews at key stages. This waterfall method works well for slow-moving, simple projects. But it falls short against the demands of frequently changing projects in a competitive environment.
Some energy and resource companies are beginning to deploy Agile methodologies to shorten the engineering cycle and expand the owner’s role from a reviewer to a more active participant. Agile speeds up the cycle by bringing cross-functional teams together, with experts from the areas that should have a voice in the design, including construction, sustainability, planning, and control.
One global mining company experimenting with Agile found that it helped cut the basic engineering cycle of a project in half while reducing staff hours by 40%. The active involvement from other related functions resulted in a simpler and more capital-efficient design. Scaling the methodology across the entire engineering team will require a big transformation, with changes to the operating model and procurement processes.
Another company used Agile teams to improve the design of a conveyor belt system for carrying materials out of a mine, cutting 15% off the cost. Among the innovations that a cross-functional team contributed: instead of lining the belt’s corridor with a series of individual lamps, each requiring its own wiring and maintenance, the design used two rows of LED lighting tape, which was quicker to install, less expensive to maintain, and distributed light more evenly throughout the corridor. Others are using Agile in early stages like concept definition and contractor selection, shortening the time to evaluate trade-offs and learning how to determine the minimum amount of information necessary to make good decisions.
Of course, in the mission-critical designs that make up most projects in the sector, Agile methodology can’t mean abandoning good governance. But companies experimenting with Agile are finding that it works well within the bounds of a traditional stage-gate process.
More transparent procurement
Traditional procurement entails bidding on unit-cost or lump-sum contracts to get the best rate at the lowest risk. But these contracts carry a fair amount of uncertainty and risk, so construction companies usually build a cushion into their bids by padding the price of labor, materials, or other general costs, or by stretching the schedule.
These risk-adjusted prices then become the baseline for the contract’s management, and both the contractor and the construction manager will direct the project according to these inefficient targets. Inevitably, unforeseen costs arise, and these get added on top of the already inefficient base. Organizations wind up running on contracts based on unknown risks, lax yields, and long schedules.
A better way to manage procurement is to analyze contract costs based on benchmarks and reviews. A cross-functional team, with people from engineering, procurement, construction, and supply, should lead negotiations with contractors. Negotiations should be transparent and technical, structured in ways that ensure the contractors understand the scope and context of the project, and include open discussions on construction methodologies, yields, and staffing requirements. When owners also take on the risks that the contractor can’t manage―such as interference from other contractors or with operations―they can manage these conflicts better, reducing costs and making construction more efficient.
Construction: Red is good
Engineering and procurement both set the stage for the most difficult phase of any project, construction. While other sectors have significantly raised productivity over the past two decades, construction is an outlier (see Figure 3).
One reason is that construction has been among the slowest sectors to embrace digital technologies―though that’s beginning to change. Building information modeling (BIM), advanced work packaging (AWP), and connected worker solutions are among the initiatives that construction companies and their customers are deploying to make their capital projects more efficient. But companies also need to find better ways to work with their contractors to boost productivity and shorten construction schedules.
Construction is the rare sector whose productivity has declined since 2000
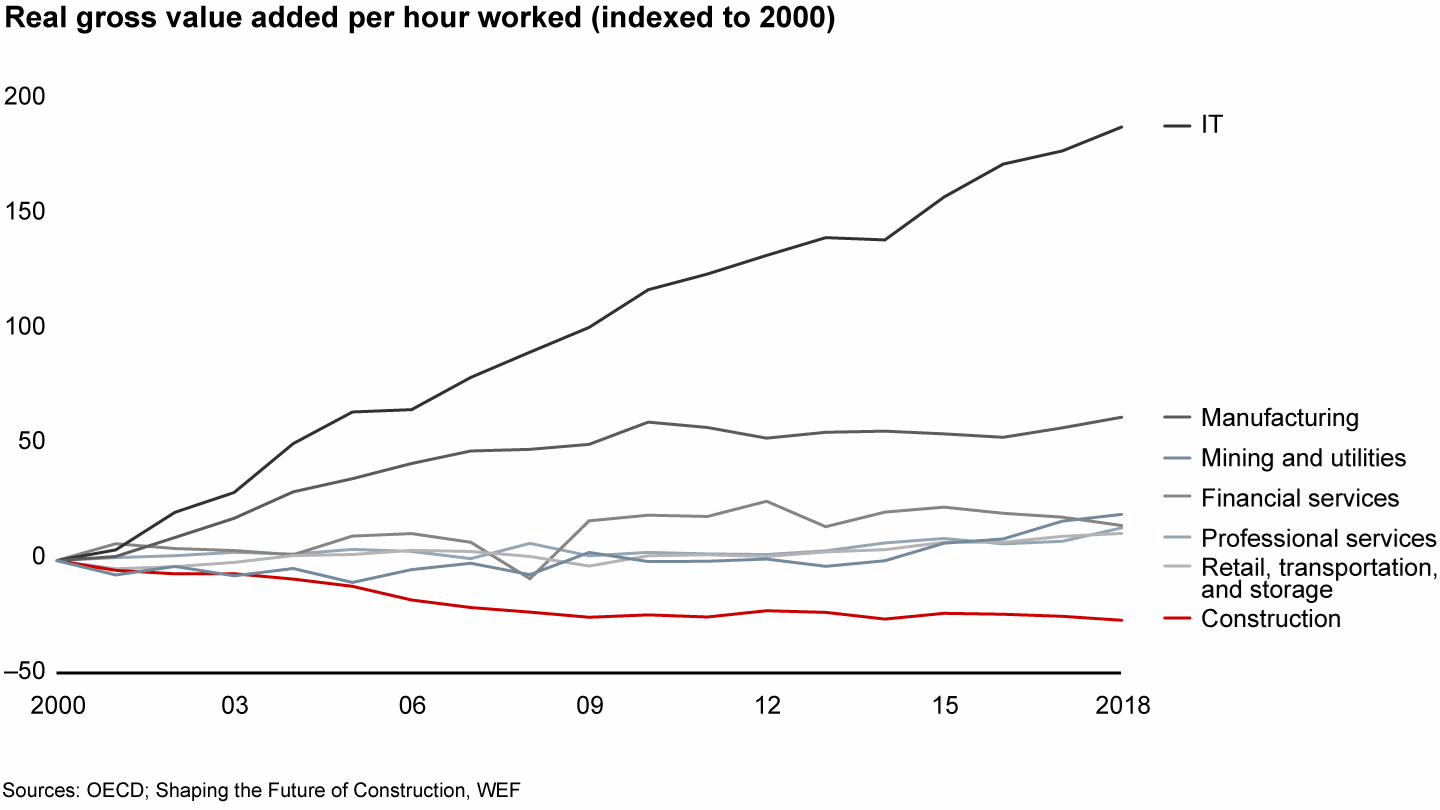
One way they can do this is through joint reviews of the construction schedule, examining the sequence, construction methodology, and productivity yields. They set the target by building a schedule based on ideal conditions, then work to meet those milestones. To make daily progress on this full-potential schedule, they follow daily routines, hold weekly obeya meetings (war room sessions to review progress, causes of noncompliance, and the next week’s plan), and employ other continuous improvement techniques borrowed from lean manufacturing. Contractors and construction managers meet weekly to discuss progress on the sequence and yields, and how to clear barriers that are hurting productivity.
Of course, all this is easier said than done. Accomplishing it requires a shift in mindset among the leaders of the construction contractor and construction management teams, and their sponsorship must be reinforced and transparent to everyone on the team. Leaders adopt a "red is good" mentality: workers who flag something that is off track or falling short are praised rather than punished, because it allows the project leaders to identify problems and opportunities for improvement. One mining company that adopted these construction management techniques recovered about 12 months of lost time, saving more than $500 million and putting the project back on track to finish ahead of schedule.
These dramatic increases in productivity and efficiency are the kinds of change that energy and natural resources companies should aspire to if they want to lead the transition to a more sustainable, low-carbon economy. The record is mixed, and this path requires openness to new ways of working and a collaborative mindset. But the opportunity is huge, and the path forward is clear and achievable.
Read our 2021 Energy and Natural Resources Report
More from the report
-
Two out of Three Won’t Do
-
Harnessing the Energy and Resource Transition
-
Net Zero: From Political Targets to Industry Action
-
Energy Is Only One Part of the Sustainability Transition
-
Redesigning Value Chains to Deliver More Sustainable Goods
-
Time for ESG Investors and Energy and Natural Resources Companies to Work Together
-
Business Opportunities in Low-Carbon Hydrogen
-
Raising Productivity in Energy and Natural Resources Capital Projects
-
Creating Resilience, Sustainability, and Accountability in Supply Chains
-
Engine 2: How to Grow a Sustainable New Business
-
Accelerating the Journey to Net Zero
-
Four Ways to Scale Digital in Energy and Natural Resources Companies