World Economic Forum

Executive Summary
- Reliability and efficiency in supply chains were prized over resilience and sustainability for decades.
- Companies need to be able to trace items across their supply chains to build resilience and sustainability.
- They will need to collaborate and share information across their industry to achieve these goals.
This article originally appeared on the World Economic Forum.
COVID-19 dealt a final blow to supply chains that only prized reliability and efficiency. The pandemic shattered brittle supply chains around the world and thrust resilience—the ability to heal, reroute or substitute—to the top of the agenda for supply chain executives.
For decades, reliability and efficiency were the dual priorities of supply chain organizations. But the price of focusing almost exclusively on dependable supply at the lowest cost was supply chains that became inflexible and opaque. And resilience wasn’t the only sacrifice: the goal of sustainable supply chains— those that embed environmental, social or corporate governance considerations as raw materials are sourced, converted to products and delivered to market—also remained elusive.
Without visibility into how materials and goods entered and moved through those chains, it was difficult if not impossible for companies to effectively police those inputs and outputs for sustainable practices. Even today, Bain & Company estimates that up to 60% of executives have zero visibility into items in their supply chain beyond their first-tier suppliers. With almost no data to evaluate trade-offs, sustainability often lost out to reliability and efficiency by default.
Now, however, resilience demands that companies are able to see what is happening everywhere in their supply chain and trace any item in it—from field to factory to customer (and beyond). And, as it happens, those same capabilities are also exactly what companies will need to integrate sustainability into their core supply chain design. The same tools that support resilience can also underpin sustainability efforts. And those tools can provide the data to accurately evaluate trade-offs between cost, reliability, resilience and sustainability—or reveal that trade-offs aren’t even necessary.
The twin engines of resilience and sustainability
Visibility describes the degree to which a company can see exactly what's happening within its supply chain, which may include real-time insights and analysis and predictive problem solving. Traceability refers to the ability to follow the exact path and process of every input, including provenance and origin information, as well as insights into the conversion process and certifications.
To achieve the visibility and traceability that resilient supply chains need, companies are adopting so-called “control towers.” Today’s control tower solutions range widely in technical sophistication. Some provide real-time data across the full supply chain and can predict sub-optimal events or disruptions, while less sophisticated ones focus on limited portions of the supply chain, with batched data, and less ability to predict. With the right data and deep transparency, control towers can not only boost resilience, they also make it easy to embed sustainability into the overall supply chain decision-making across both the inputs to the supply chain and the corresponding conversion processes (see Figure 1).
Traceability and visibility improve supply chain performance across the board
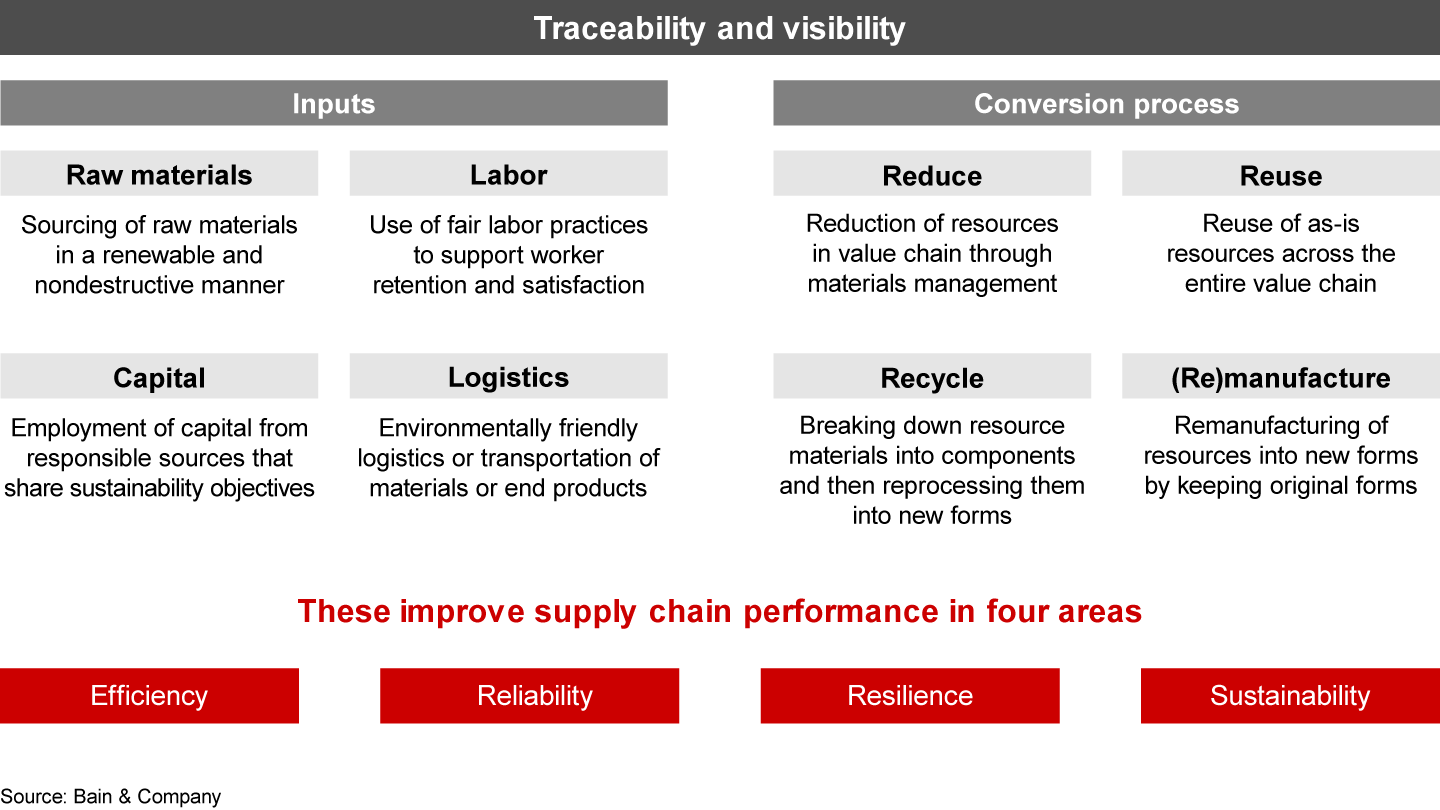
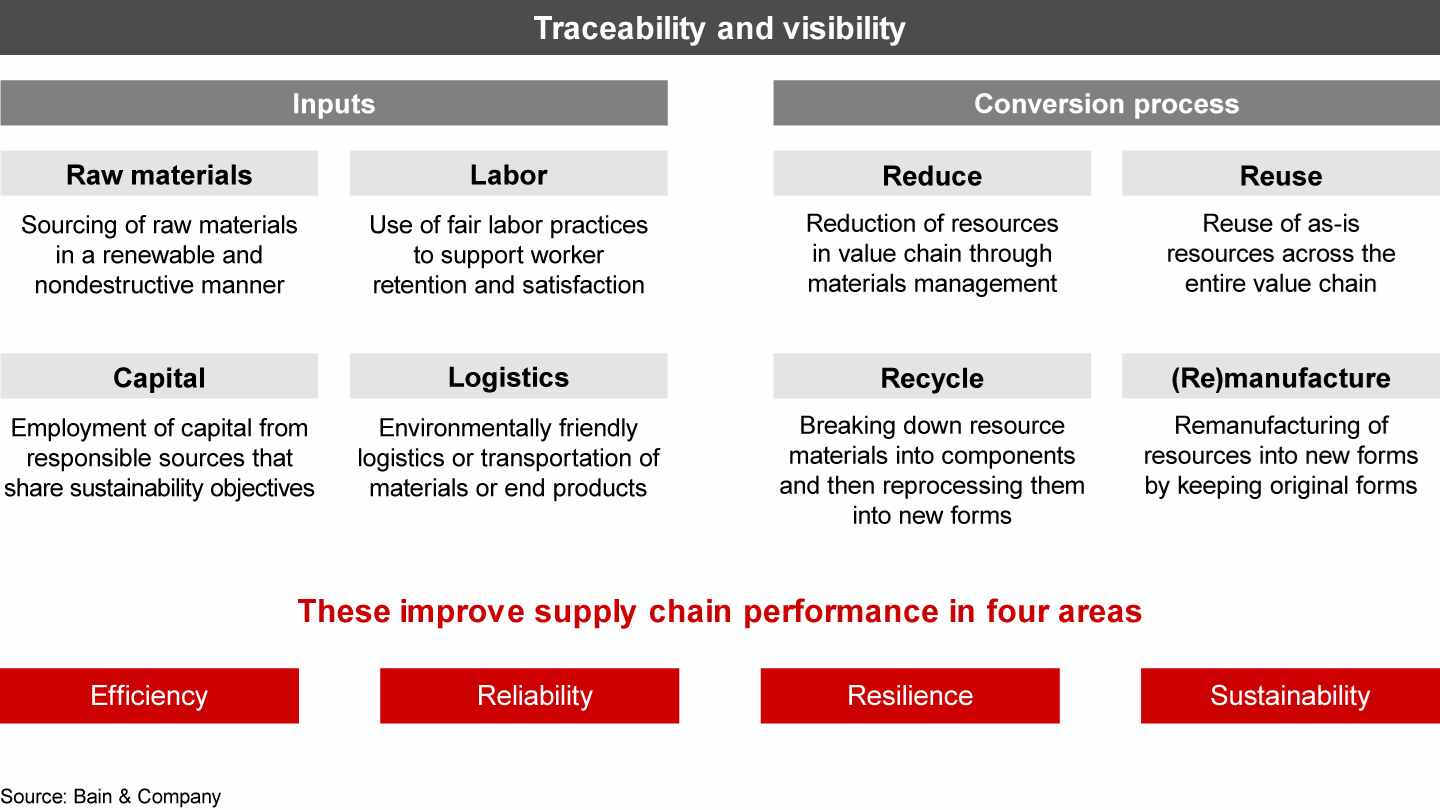
This traceability is essential to meet the increasing push for circular supply chains that recapture and reuse raw materials at the end of a product’s lifecycle. Tracing materials throughout the product lifecycle is a prerequisite for feeding it back into the conversion process for reuse, recycling, or remanufacturing. Each cycle reduces the consumption of raw input materials. These circular supply chains are not limited to circularity within a single company’s value chain. Often, materials are recycled by third parties and later fed into another sector’s value chain as substitutes for the virgin raw materials. Visibility into supply and demand are also critical for companies to seize these opportunities.
The path to visibility and traceability
In the context of the Great Reset, this is a critical time for the evolution of supply chain visibility and traceability. But most companies have a long way to go. According to a recent Bain survey, fewer than 15% of executives feel their current capabilities allow them to deliver traceability consistently. A majority of companies have started to build some traceability capabilities, but struggle to integrate them or consistently create value.
The most common reasons were data barriers, including unreliable data from supply chain partners and a lack of standardization for data exchange and the calculation of metrics. There are also technological barriers, such as the absence of end-to-end platforms, and organizational barriers, such as untrustworthy data-sharing mechanisms or privacy concerns.
Overcoming these hurdles to resilient and sustainable supply chains will require collaboration among multiple stakeholders within a sector, both to set standards and fund platform-type investments, as well as to focus resources, share costs, and gain traction. If multiple players in a sector can align on a common language, standards, or data model, all will benefit from accelerated capability development, less decision complexity, easier benchmarking and other forms of collaboration.
In recent years, several sectors have combined forces to accelerate traceability and visibility. For example, IBM’s Food Trust, founded in 2017, addresses the need for smarter, safer and more sustainable food supply systems by connecting an ecosystem of producers, suppliers, manufacturers, retailers, and other stakeholders. The blockchain-powered solution helps participants eliminate supply chain bottlenecks, enhance their reputation for quality, ensure safety and regulatory compliance, and build a sustainable supply chain with less waste and spoilage.
If industry-wide sharing and collaboration are the future, how do we get there? Our view is that industry leaders—moving ahead of regulators—will likely push the initial development of the platforms and set the standards, then be joined by other industry players who see the value. These leaders can consider and act on four key steps:
1. Create an environment for sharing data, experiences and best practices. To achieve sector-wide adoption, these efforts will likely require the involvement of trusted neutral entities, such as industry associations. While only 6% of executives surveyed feel comfortable sharing supply chain data with competitors, two-thirds are comfortable sharing with industry associations.
2. Bring the digital platform to life for multi-stakeholder collaboration. A technology company will likely need to shoulder the ongoing hosting and development of the platform, then commercialize the solution.
3. Create trust in certification. Certification providers can verify the inputs and processes of each platform participant, the digital platform itself, or the analytical results it produces in a trusted way.
4. Develop a toolkit to effectively mobilize and create value. Every company involved will need a playbook for how to build the required talent, systems, and processes; guidance around how to benchmark performance, progress, and development against the sector; and clear roles and responsibilities for deriving business value, resilience and sustainability from the newly available insights.
We expect industry leaders will be prescient enough to avoid the potential paralysis that comes with too broad a scope and instead focus pilots on solving one big issue before moving on to the next. As additional participants, even competitors, join the effort, sectors can work together to ensure efficient, reliable, resilient and sustainable supply chains.