Etude

At a Glance
- Manufacturing vacancies in the US have reached a record level.
- Nearly 50% of the US manufacturing workforce is age 45 or older; 25% is 55 or older.
- Flexibility and other nonmonetary benefits are critical to attracting and retaining workers.
At one large US manufacturer with more than 1,000 job vacancies, labor shortages are puncturing robust growth. For decades, workers lined up to work for the company. Now, the gap between job vacancies and willing recruits is so vast that executives say they can’t produce enough to meet demand. Adding to the frustration, 25% of new hires either don’t show up for work or quit within a short period of time. The opportunity cost of that talent shortfall is immense: If the firm could fill its job vacancies, sales would be 30% higher.
Labor shortages are on the rise around the world, and at many US manufacturers, they have reached a crisis level. Companies unable to fill hundreds or thousands of jobs openings are suffering declines in growth and profitability. Manufacturing vacancies in the US soared in July, to 906,000, an all-time high since the US Department of Labor started tracking them in 2001 (see Figure 1). At the same time, Americans are quitting their jobs in record numbers—34.5 million left their jobs during the first nine months of 2021. Manufacturers in September 2021 had 85% more job vacancies than hires, far greater than the overall US level of 55% in the private sector. In Europe, manufacturing job vacancies also rose sharply in 2021.
Covid-19 triggered a sharp increase in manufacturing labor shortages
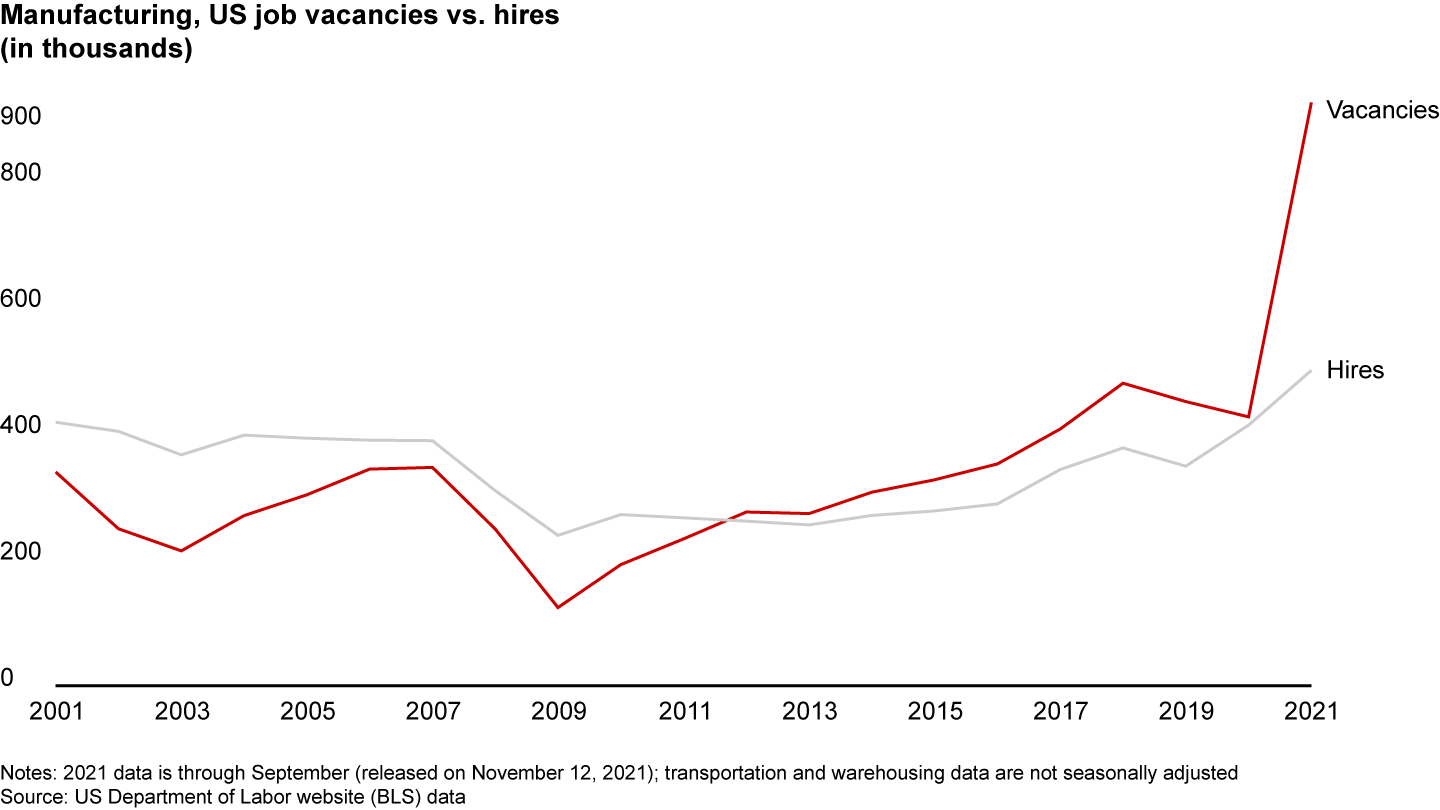
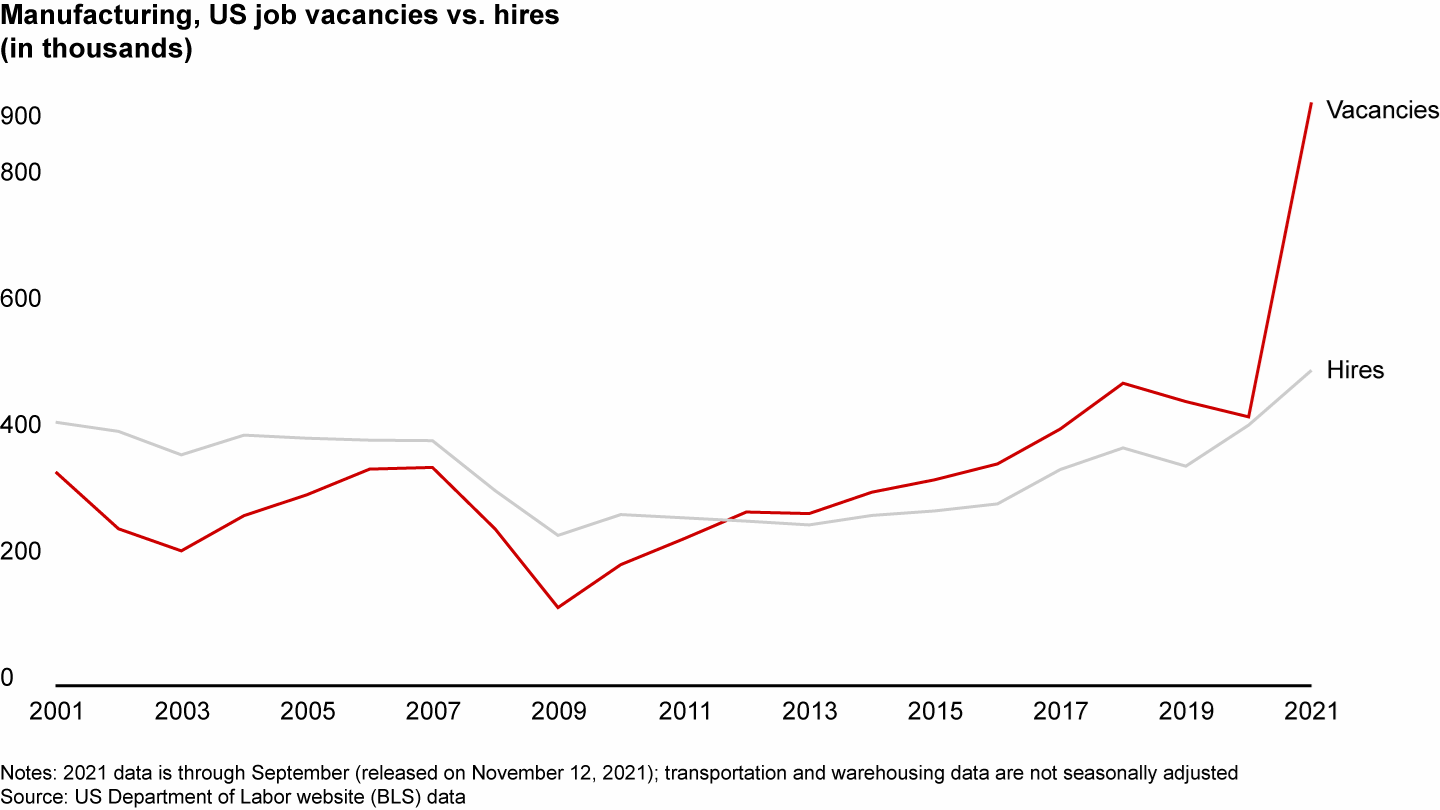
It’s a dilemma most companies never anticipated. Unaccustomed to sharp swings in labor availability, human resources teams at stricken firms have no process in place to rapidly hire a huge number of workers. The bad news is that in many countries around the world, labor shortages are likely to worsen in the coming decade, with demographics fueling the trend.
Nearly 50% of the US manufacturing workforce is age 45 or older, and 25% is 55 or older (Figure 2). In the EU, 16% of the workforce is 55 or older, and in several countries, including Germany, Finland, and Sweden, the rate is nearly 20%. As baby boomers and Gen X workers reach retirement age, the supply of labor will shrink further. China already has lost 5 million workers from the labor force over the past decade because of a declining birthrate. Companies that fail to quickly rethink their hiring and retention strategies may fail to meet growth and profit targets.
An aging workforce and the shift of Gen Z workers away from factory jobs will intensify the labor crisis in manufacturing
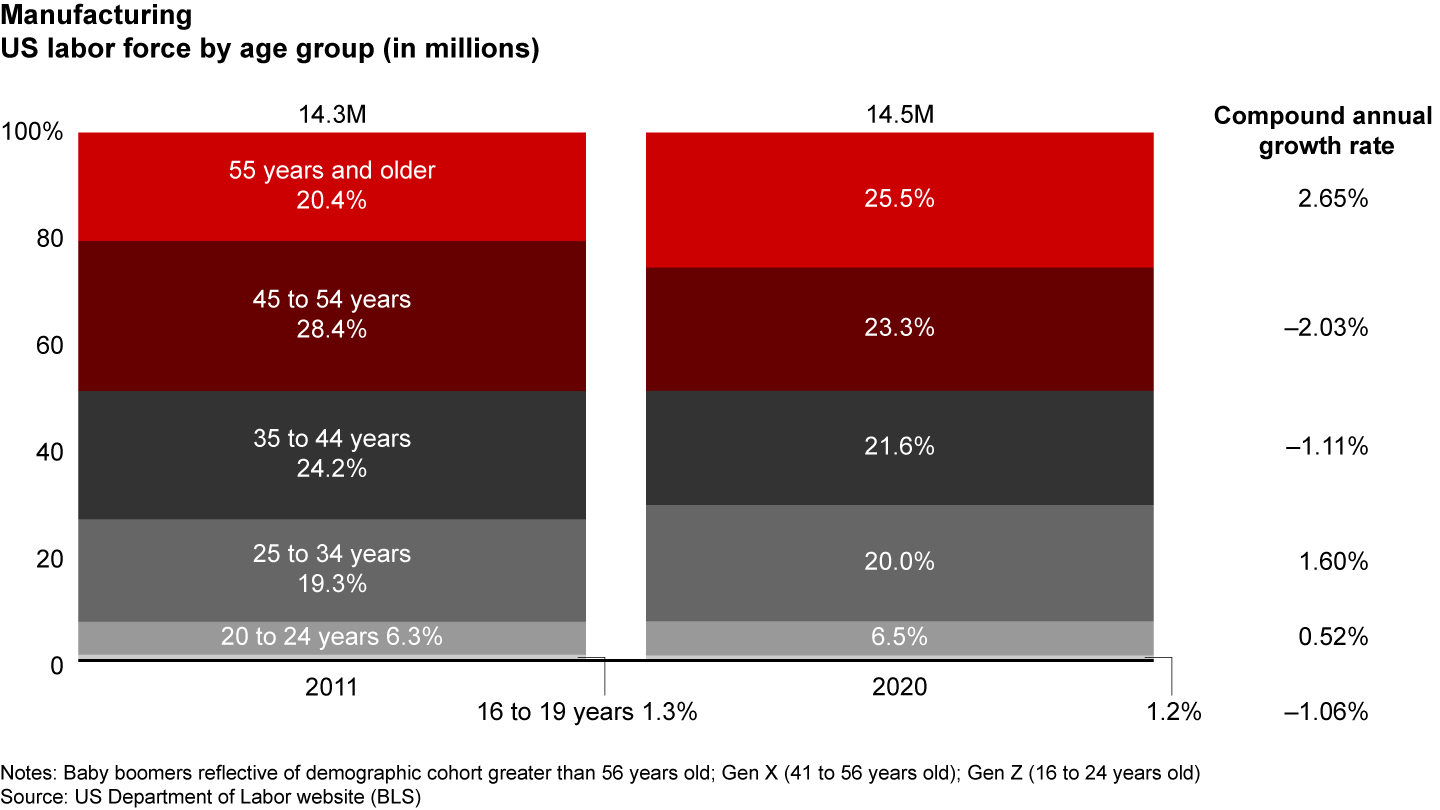
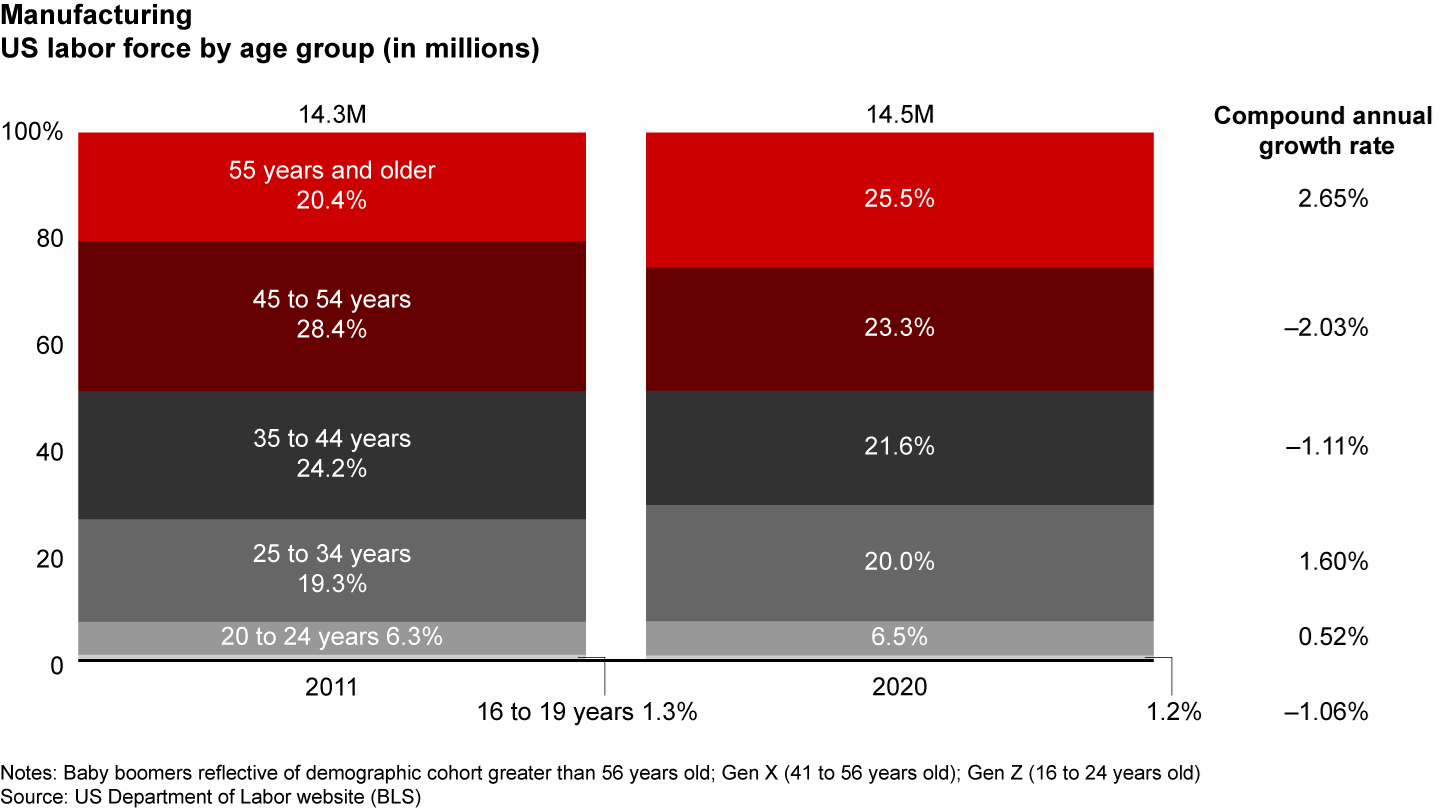
Labor shortages are likely to persist for several reasons. The US workforce is aging while the labor participation rate has declined and is now stagnant at around 61% of the population. At the same time, demand for manufactured products is rising. In the short term, the pandemic has spurred consumers to shift spending from services to goods, boosting demand for products such as furniture and automobiles. Longer term, corporations and public organizations are planning to repatriate manufacturing in response to geopolitical tensions, and the US government is offering incentives to those who do. Repatriated plants will increase the demand for workers. The recent US Innovation and Competition Act, for example, earmarks $52 billion to spur domestic production of semiconductors and $10 billion for new technology hubs throughout the country.
Covid-19 triggered a chain reaction in the labor market, amplifying the existing trend. As the pandemic interrupted global supply chains and production, companies furloughed or laid off millions of workers—and many have not returned to their former jobs. Three million excess US workers retired during the pandemic, and they are not likely to rejoin the workforce. Spending more time at home throughout the pandemic also convinced some factory workers that they no longer want to put up with the inflexibility of manufacturing shiftwork. As a result, the US job market is now roughly 3 million workers short of demand.
Before the pandemic, younger workers already were gravitating to e-commerce warehousing or transportation jobs as well as gig economy sectors such as ride sharing and food delivery rather than manufacturing. Millennials, in particular, place greater value on leisure time and family, ranking workplace flexibility as a top priority (see Figure 3). Thirty percent of US workers freelance, and 65% of them make more money doing so than in traditional jobs. That’s one reason a growing percentage of younger workers view gig economy jobs as full-time career options.
Flexibility and other nonmonetary benefits are critical to attracting and retaining workers
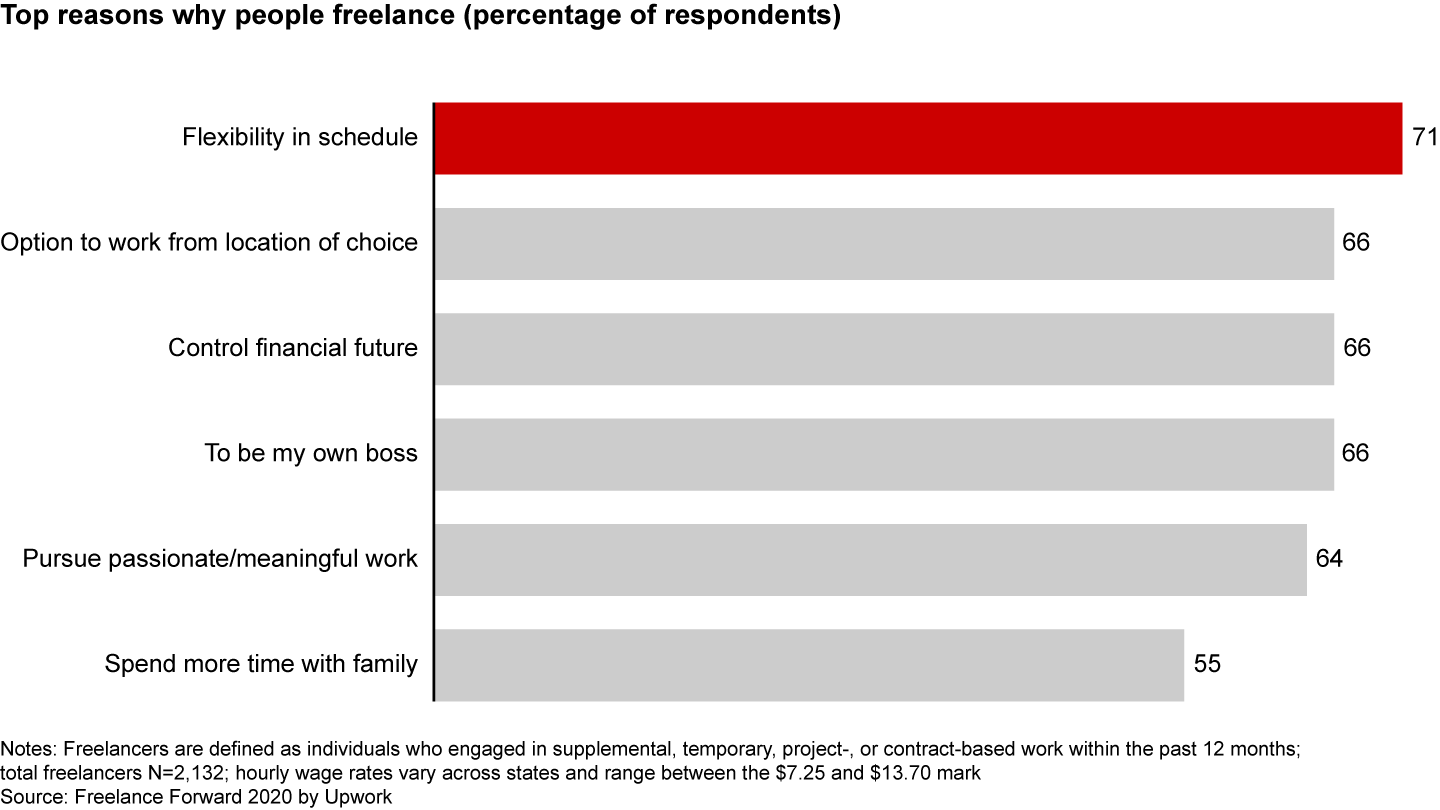
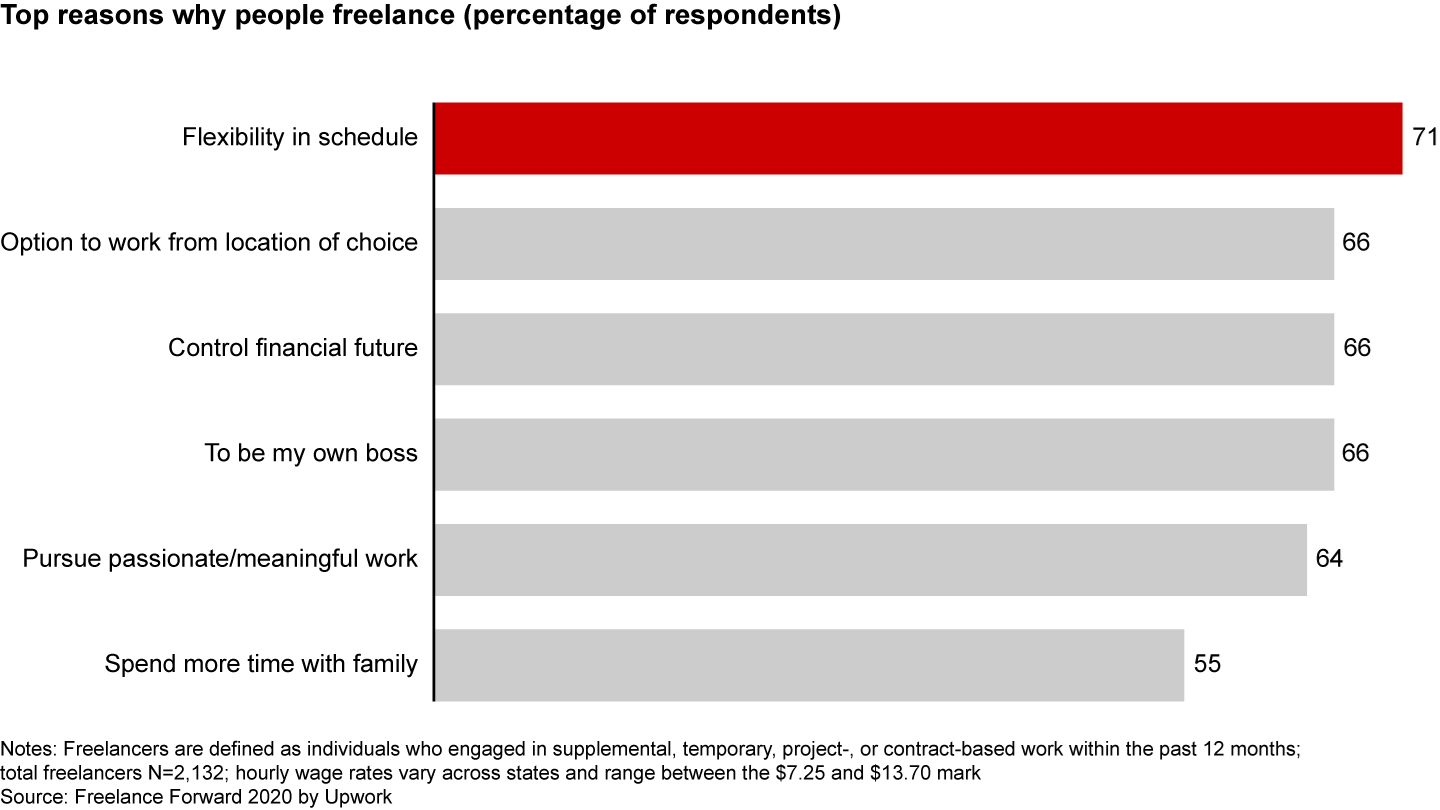
Manufacturers also have lagged in using technology to reach potential job candidates. Digital-savvy companies such as Amazon and Uber are highly effective at wielding social media to appeal to younger workers. And many industries have recognized that social media is critical to attracting qualified and younger candidates. Hospitality giant Marriott, for example, posts engaging content twice a day on its online career page and offers dedicated entry points for veterans, students, and grads. The company also encourages employees to chat with job candidates on its career page and provides advice on applying for a position. Marriott’s career Facebook page has about 1.35 million likes.
Raising wages should be an obvious strategy to attract workers. Since the onset of the pandemic in March 2020 through October 2021, however, US manufacturers have increased hourly wages by an average of 8.7%, and shortages have not eased. Raising the bar for competitors, some companies also are offering hefty signing bonuses and significantly expanded benefits to lure workers, including college tuition reimbursement. And manufacturing employees are being lured away by companies in other nonmanufacturing sectors. Companies that don’t look beyond their own industry and match broadly improved salary and benefit packages stand little chance of filling open posts.
Finally, the conventional workplace environment in the manufacturing industry makes it difficult to attract young recruits. Its workforce and senior leadership historically have been predominantly male (70%), white (80%), straight, and cis-gendered. For a growing percentage of the population, that profile does not reflect the whole of society, making the traditional manufacturing workplace a less desirable career option. The ZipRecruiter platform, for example, has seen a 220% year-over-year increase in searches including the word “diversity.”
Forging a new labor strategy
The coming decade will test the ability of manufacturers to develop local labor pools and to rethink recruiting and retention. For the first time in decades, workers are in the driver’s seat when it comes to selecting an employer. Leading companies already are implementing a series of short-term and long-term measures to minimize the impact of chronic labor shortages.
Four short-term actions can begin to reduce the yawning gap between job vacancies and available workers.
Invest in individuals. To attract workers in a tight labor market, companies need to continually update compensation packages, ensuring salaries, benefits, and incentives track with changes in the market. But leading manufacturers are going beyond this table-stakes move to rethink the broader employee value proposition. They are designing more compelling career progressions for current and prospective employees, and they are retooling schedules to incorporate more flexibility and more stable shifts. These moves can help attract different talent pools that may not have considered manufacturing jobs in the past. And to compete with the gig economy, some companies even offer gig economy benefits such as same-day pay.
For example, Walmart, America’s largest employer, recently offered to pay all college tuition and book costs for its entire workforce of 1.5 million employees, including part-time staff. The company plans to invest nearly $1 billion over the next five years in career-based training and development.
Many companies also are introducing more flexible working arrangements, including shift swapping, short work weeks, job sharing, and flexible hours. During the pandemic, aerospace giant Rolls-Royce rolled out new ways of working, including split shifts and dynamic schedules to ensure labor availability.
Optimize your portfolio. The pandemic forced many companies to simplify their offerings and focus on the most popular, fastest-moving items. Streamlining the portfolio, in turn, reduced supply chain complexity and labor needs. Many companies suffering from labor shortages are now applying that lesson in a new setting. Pandemic-induced shortages have made consumers more focused on availability and less concerned with variety. That’s an opportunity to rationalize product variants and stock-keeping units (SKUs). Fewer SKUs means lower cost, complexity, and inventories. Global snack food maker Mondelēz, for instance, decided in 2020 to reduce its SKUs by 25% to sustain pandemic market share growth.
One global consumer healthcare company increased revenue and gross margins significantly by optimizing its portfolio during the pandemic. Faced with a 30% to 40% rise in demand for its products, senior management launched a review to identify low-performing and inefficient SKUs as well as those that increased manufacturing complexity. Ultimately, the company streamlined the total number of SKUs by 40%, a move that increased production capacity by 10% to 20%, boosted revenue significantly, and increased margins by an average between 200 and 300 basis points.
Rethink hiring guidelines. Leadership teams also can expand a company’s potential labor pool relatively quickly by reshaping hiring guidelines. For instance, consider recruiting people from different geographies or people with disabilities. Some local authorities and companies are collaborating with nongovernmental organizations to help fill jobs. The International Rescue Committee in Utah has helped to resettle 12,000 refugees in the state since 1994, including Afghan refugees. And The Welcoming Center in Philadelphia places skilled immigrants, refugees, and asylum seekers with work visas in jobs. Companies interested in targeting a broader potential workforce, including recent immigrants, should ensure support for non-English speakers, including bilingual supervisors and work instructions in multiple languages.
Harness new technologies and communication channels. To reach a broader percentage of potential job applicants, companies are using digital on-demand staffing platforms, such as Bluecrew and Shiftgig, to fill talent pipelines. These platforms connect gig economy workers to opportunities across multiple industries, including manufacturing. The benefits: real-time labor availability from a pool of candidates willing to work but who don’t necessarily want to make a long-term commitment.
While short-term measures can help ease the immediate crisis, successful companies also are developing long-term strategies to ensure that they are better positioned for a tight labor market in years to come. Broadly, three actions can help companies minimize chronic job vacancy problems in the future.
Create state-of-the-art training programs. Leading manufacturers are partnering with community colleges and other local community organizations focused on training and job placement. The goal of such programs is to create a steady pipeline of qualified workers with the technical skills needed in an Industry 4.0 landscape. That will be increasingly important as the next phase of automation increases demand for skilled workers to oversee automated production lines.
Pacific Gas and Electric (PG&E), for instance, offers a free, eight-week PowerPathway training program in partnership with several California colleges, the Aspen Institute, and veteran organizations. The program ensures that potential job applicants have the academic and job-specific skills required in the energy and utility industry. Classes are taught by PG&E instructors and include training in the field. Since the program’s launch in 2008, more than 1,000 people have graduated from the PowerPathway program, and 82% have been hired by PG&E or within the utility industry. Nearly 50% of graduates are veterans, and 68% are people of color.
Invest in automation. As labor shortages become chronic and labor costs rise, companies have an increased incentive to invest in automation. Automation technology can help companies stay productive and competitive in a tight labor market. A second wave of automation is likely to transform manufacturing industries at a quicker pace than what was anticipated just a few years ago, reducing manual labor requirements but increasing the need for people with technical skills to manage a more automated production system. In the first nine months of 2021, orders for industrial robots by North American companies hit a record $1.48 billion.
In March, grocery giant Kroger opened the first of 20 planned large warehouse and distribution centers across the US manned by hundreds of robots designed to bag groceries for delivery to customers. The robots can assemble an order of 50 items in 6 minutes, compared with the 30 to 45 minutes it takes for a Kroger employee to pick goods off the store shelf. And Domino’s Pizza is investing in equipment and technology that reduces the amount of labor required to produce pizza dough balls.
Chinese manufacturers also are investing in automation as they cope with a growing shortage of workers. China’s workforce has shrunk by 5 million people over the past decade in the wake of a declining birth rate. Midea, a home appliance giant in southern China, is increasing factory automation at its 34 plants, anticipating that an aging population will further limit the labor supply.
Before investing in automation, successful companies train or hire the skilled staff needed to operate and maintain the technology. They also ensure that teams in operations, research and development, and sales work together to understand and manage the complexity of new products.
Explore smart factory solutions. Companies facing labor shortages or a lack of workers with the right technology skills are deploying innovations such as computerized, remote operations; 3-D printing; and technology-augmented solutions. Australian mining companies have hired remote operators in cities to supervise automated mining operations located in isolated areas. That includes, for example, using computer systems to oversee self-driving trucks that work 24/7 and making sure that they meet their production targets. Locating such operations in cities with a sufficient population base helps to ensure a larger supply of labor for jobs that otherwise may be difficult to fill. As companies grapple with a higher level of talent turnover than in the past, new technologies may also assist workers by filling in for missing skills or technical capabilities.
Finding a rapid solution to the shortage of workers has become the No. 1 priority for many operations executives. For the first time in decades, workers are flush with opportunities and are commanding far better compensation and benefits than in the past. Organizations that quickly adjust their strategies to this new reality will have an inside track on filling those vacant jobs and energizing their workforce.