The Situation
AutoCo* is a major automotive manufacturer whose large vehicle group is extremely profitable, but customer demand for these vehicles exceeds existing capacity
AutoCo's large-vehicle production is constrained by engine output. Executives want to increase the rate of engine production by five jobs per hour.
Plant management determined that XYZ Assembly* was the primary obstacle to achieving the engine production necessary for the target number of vehicles.
As part of a full potential manufacturing improvement program, AutoCo charged the Bain team with:
- Improving productivity at the bottleneck machine on the main assembly line
- Improving the yield of the subassembly department feeding the bottleneck machine
- Finding five more engines per hour (JPH) on the XYZ Assembly and on the mainline station it feeds
Our Approach
For each machine, Bain deconstructed the manufacturing process to uncover the highest priority drivers of cycle time.
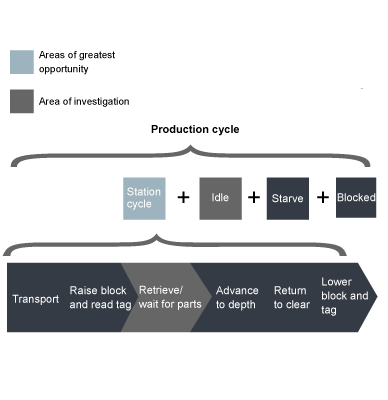
Our Recommendations
The team focused on a 1.5 second-per-cycle overrun that occurred 75 percent of the time and yielded an 11 JPH loss.
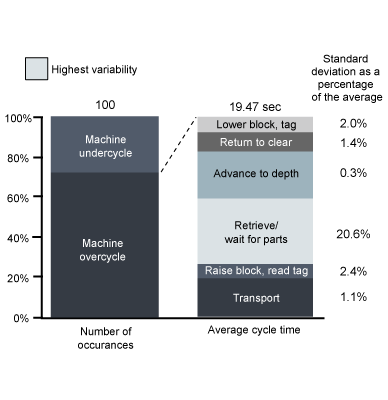
The Results
Bain nearly doubled the client's original cycle time reduction goal and identified fuller upside potential in the assembly.
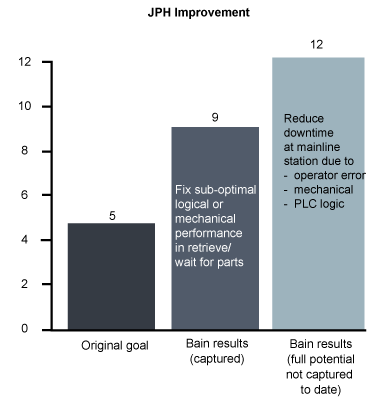
* We take our clients' confidentiality seriously. While we've changed their names, the results are real.