Brief
In evidenza
- Pharma executives are starting to experiment with smart factories powered by big data and machine learning.
- The first wave of solutions will improve production transparency, equipment effectiveness and throughput.
- Advanced planning tools can boost quality and increase supply chain flexibility.
- Key Industry 4.0 challenges: integrating new and existing IT systems and building digital skills.
As pharma executives grapple with rising complexity, costs and regulation, more of them are looking to Industry 4.0 manufacturing as a solution. Smart autonomous factories managed with data and machine learning will lower pharma manufacturing costs, improve quality and reduce capacity constraints.
It’s a big leap. Until recently, most pharma companies have adopted digital manufacturing tools slowly, worrying that their systems, data and people weren’t ready. But many have decided further delay isn’t an option and have begun experimenting with Industry 4.0 solutions. Pharma executives expect smart connected factories to produce total savings of 20% or more, while improving quality and making deliveries more reliable. Specifically, they forecast a 17% reduction of costs related to poor quality, a 15% decline in the cost of converting raw materials into drugs and a 14% increase in delivery reliability (see Figure 1).

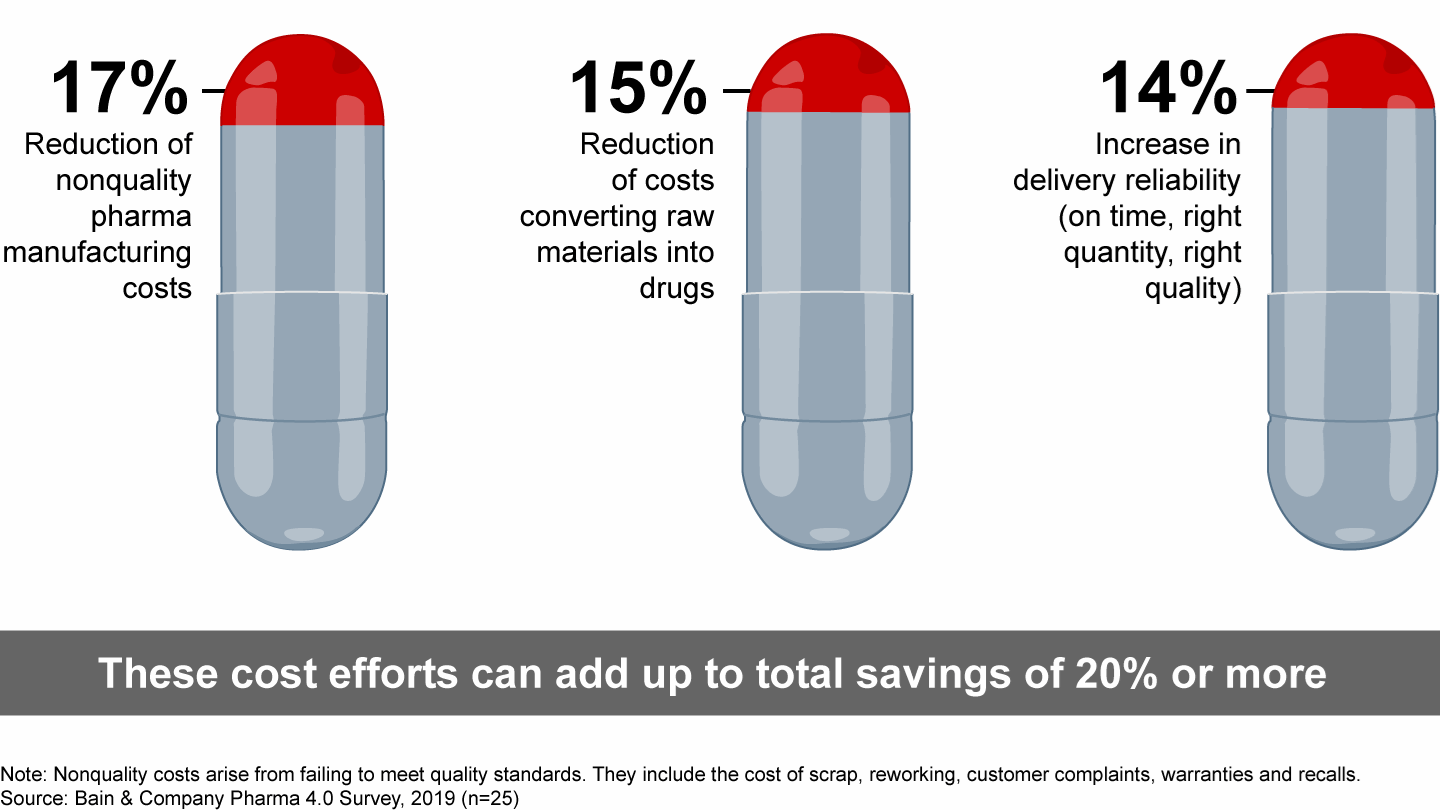
Regulatory changes, the proliferation of generic drugs and more personalized medicine put pharma profits at risk and make a strong case for digital manufacturing. Smaller, more frequent drug launches increase production complexity and costs. The emergence of personalized medicine with drugs tailored to individual patients also means more complex processes. And widespread use of generic drugs is pushing prices down.
Which of the many digital manufacturing technologies will pharma companies roll out first? We expect leading pharma companies to invest first in a cluster of no-regrets solutions based on tools that are easier to implement. Cost savings from those solutions will help fund future investments, including a second wave of high-impact solutions that are more difficult to implement. Here’s a quick look at five critical solutions in each group (see Figure 2).

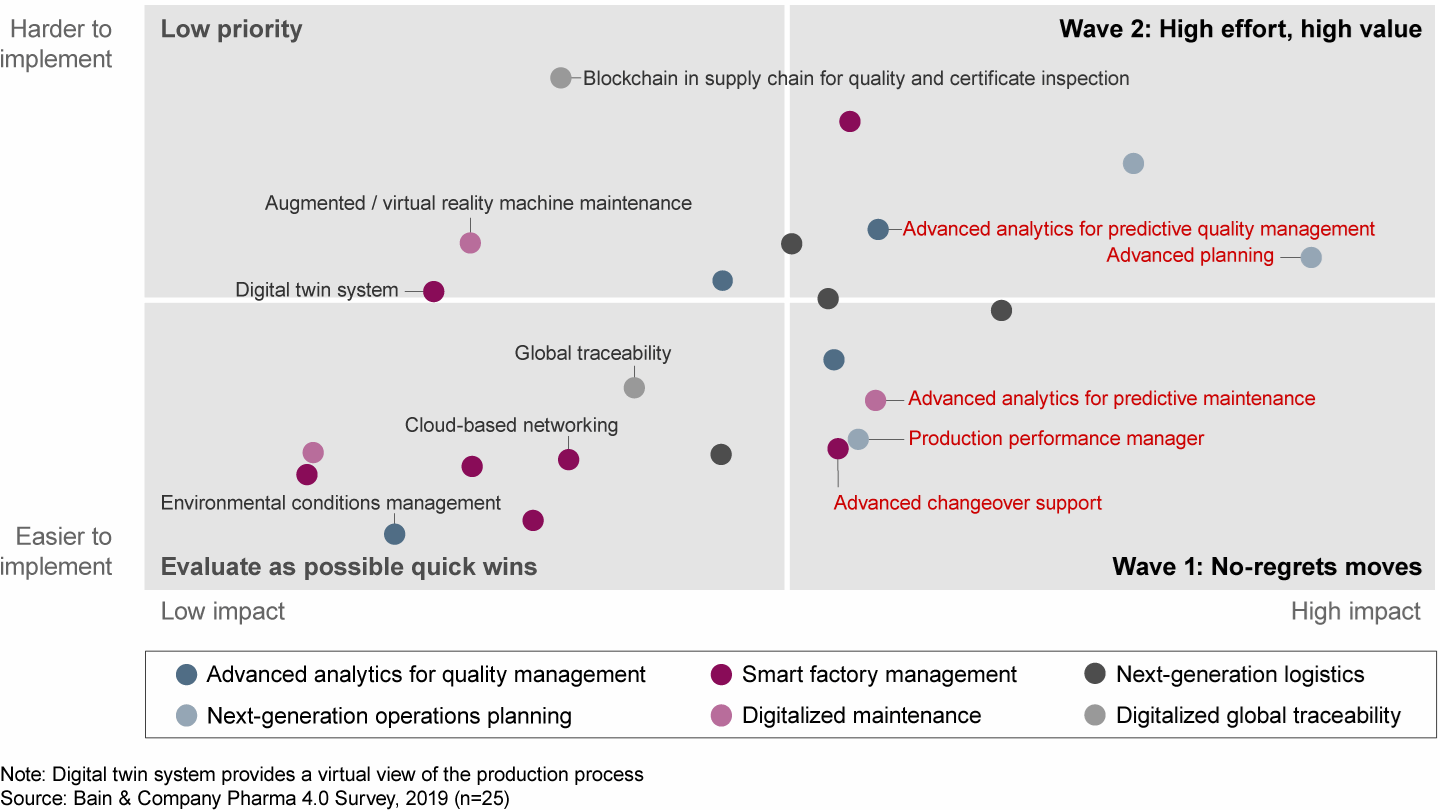
Wave 1: No-regrets moves
Production performance manager. This solution gathers near-real-time data from manufacturing equipment to produce an overview of the entire production system, including the condition of each machine. Managers reviewing the system from end-to-end can rapidly spot problems and performance gaps and use data to identify the root causes. Implementing a production-performance manager system is relatively easy for companies that already have installed a manufacturing execution system (MES) and use lean manufacturing techniques.
Advanced analytics for predictive maintenance. Using data from sensors to identify breakdown patterns—which part of a machine fails, the type of breakdown and when—this tool can predict problems in advance, giving production teams the chance to maintain machinery before it goes down. That early warning reduces production losses and helps prevent expensive repairs. And optimizing the frequency of maintenance also lowers its cost.
Advanced changeover support. When teams on the shop floor reconfigure machinery to produce different products, they need to move rapidly to reduce manufacturing downtime. Advanced changeover support guides workers during that process. Virtual-reality glasses or three-dimensional video simulations on handheld devices help operators follow a defined procedure to make changes as quickly as possible.
Wave 2: High effort, high value
Advanced analytics for predictive quality management. Even if products are within given specifications, being close to the borderline of acceptable tolerances can prompt quality issues. Recognizing patterns linked to quality problems in production, packaging and logistics can help companies react faster and avoid defects. This tool searches for patterns in production, quality control and supplier data often linked to defects and highlights the root causes of poor quality.
Advanced planning. Increasingly, companies are using big data analytics to gain insights from historical data to improve demand management, reduce inventory buffer and streamline long-term production plans and short-term schedules. This tool helps production managers determine the right resources (machines and people), inventory and sequence of production orders for a required output and service level.
Getting started
The biggest obstacle for leadership teams planning to embrace pharma manufacturing 4.0 is integrating new and existing data systems. Nearly 85% of pharma executives we surveyed cited that effort as the No. 1 implementation challenge. Sixty-four percent ranked behavioral changes required for digital manufacturing as the next-biggest challenge. The third obstacle was a lack of required skills among employees.
Leading companies follow four guidelines when implementing Industry 4.0 technologies.
- Define and manage the change as a business transformation, not a digital transformation.
- Take a pragmatic approach to scaling new technologies. Chose those that deliver a quick return and the best results.
- Invest in people and capabilities for digital manufacturing.
- Partner with best-in-class solution providers and learn from other industries.
Industry 4.0 technologies will change pharma manufacturing processes dramatically in the next five years. Companies that get started now will have a head start in creating a competitive advantage.
Frank Lesmeister is an expert vice president with Bain & Company’s Performance Improvement and Healthcare practices, and he is based in the firm’s Düsseldorf office. Parijat Ghosh is a partner in Bain’s Performance Improvement and Healthcare practices and is based in the New Delhi office.