Brief
Utility transmission and distribution (T&D) organizations manage dozens of complex, interdependent processes, from job initiation through design, permitting, construction and job closure. Efficient execution requires close collaboration across these processes, and effective management relies on clear controls and accountabilities across the workflow.
Some T&D organizations have adopted centralized, functional organizational structures to improve efficiency and reduce costs. But despite investments in centralization, specialization, process redesign and technology systems, many executives still feel that siloed, disconnected processes and unclear ownership prevent their operations from achieving full potential.
So how can T&D leaders create end-to-end process integration and ensure accountability across functions and wide geographic areas? A common approach is to reorganize, hoping that a different structure will produce better outcomes. But unless they address the underlying processes, reorganizing merely trades one set of constraints for another. A more certain way to boost efficiency and productivity is to focus on improving collaboration, accountability and workflow among existing organizational groups.
From geographic to functional models
Historically, utility transmission and distribution organizations often comprised many local operating units that divided the territory by regions. Local superintendents oversaw all aspects of maintenance and construction, from inspection, estimating and design to construction and order closure. This structure enabled quick decision making and took advantage of local expertise and relationships. It created clear lines of accountability, as local leaders were responsible for performance in their areas. These superintendents also integrated workflow and made sure that work progressed smoothly from one step to the next.
Over time, as larger utilities acquired smaller ones, cost pressures increased and new technology systems touted the efficiencies of centrally managed businesses, many utilities reorganized T&D operations by function. Local superintendents still controlled field crews, but responsibility for inspection, estimating, design, scheduling and work preparation shifted upstream to functional leaders who supervised these activities across all geographies. Utilities hoped this centralization would deliver several benefits, including reduced head count and workload balancing across regions, higher service levels due to better specialization and expertise in functional areas, and improved performance from standardizing processes and sharing best practices.
The functional structures, however, imposed new problems. Local operators felt they were less able to be responsive to requests in their areas because they had to be routed through centralized offices. Functions became siloes with limited communication and collaboration across planning, design and execution teams. Accountability became more elusive, and cost overruns or missed deadlines led to finger pointing across functions. Transmission and distribution organizations created new positions, such as expeditors, coordinators and cross-functional program managers to address the gaps, but that reduced the cost savings they had hoped for and slowed processes down.
Facing the operational challenges of a functional model, some T&D executives now wonder if there is a structural solution and whether they should return to a geographic structure or organize by work type to unlock greater efficiency and productivity (see Figure 1). Our experience working with utilities suggests that, while there may be an ideal structure for a T&D organization, based on territory size and diversity, level of standardization and work mix, no structure offers a silver bullet to the challenges of communication, collaboration and accountability (see Figure 2). Reorganizing may simply swap one set of challenges for another, and unresolved problems tend to show up in new forms after the reorganization.
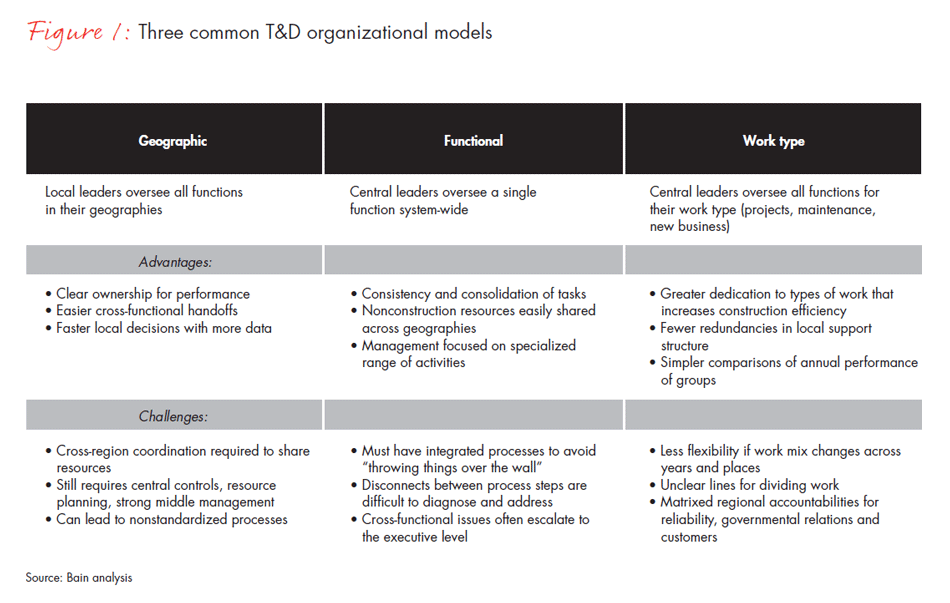
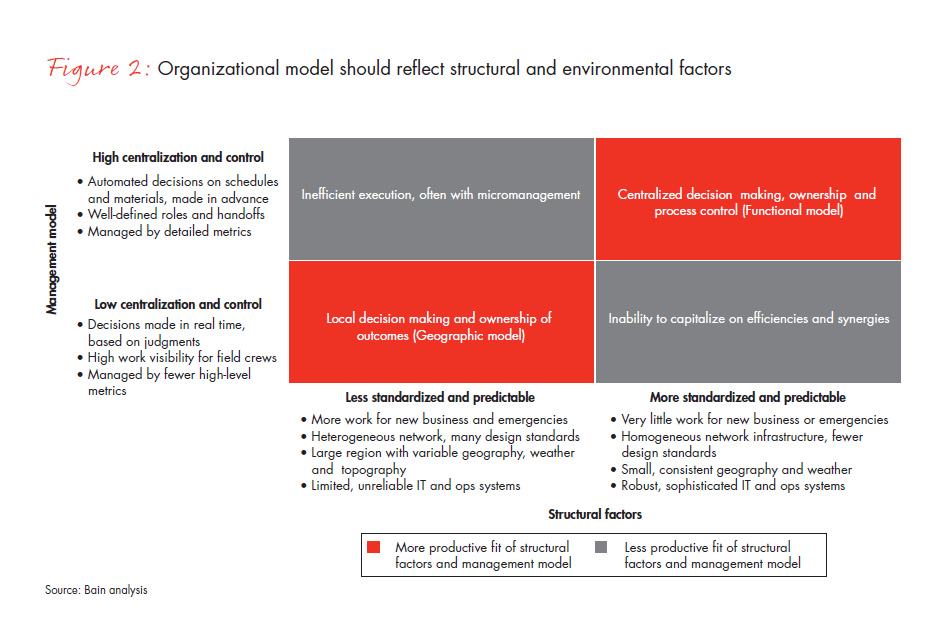
Improve performance under any organizational model
Regardless of the organizational model, three critical factors form the foundation for efficient and productive T&D operations (see Figure 3). Focusing on these issues rather than on the structural lines and boxes typically delivers greater gains in less time than embarking on a large, transformational reorganization.
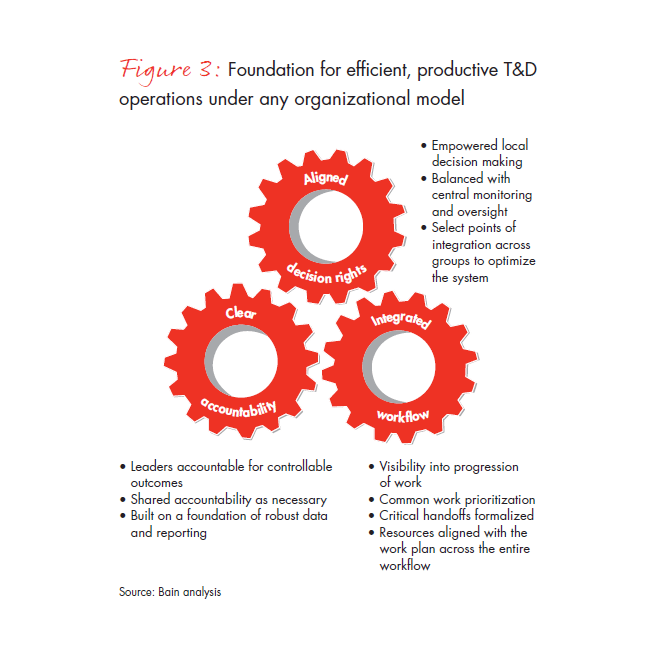
- Integrated workflow. Establish essential connection points and align priorities across organizational groups to ensure the entire system works together.
- Clear accountability. Focus on outcomes rather than process steps, with metrics tied to activities predominantly under the owner’s direct control.
- Aligned decision rights. Empower those closest to the work, but provide clear escalation and oversight to make the best decision for the company.
Integrated workflow. T&D organizations are tightly linked systems, with each department playing a critical role in overall success. Any breakdowns between groups and across functional, geographic or work-type boundaries can hurt performance. Leading utilities use three tools to ensure work flows smoothly across the organization.
- Create visibility into work progress and develop common expectations for lead times at each stage. Participants in the workflow should have an integrated view of the status of planned work, from initiation to close. A dashboard showing metrics on work volume and progression can ensure that teams across functions have common expectations for work delivery dates and cycle times at each stage of the workflow. Visibility and consensus on deadlines help the organization prioritize and address delays or bottlenecks as they occur.
- Identify and formalize critical handoffs. At one utility, local maintenance schedulers often handed small maintenance work to the capital projects organization when they fell behind, leading to frequent disruptions and delays in the project work, and reducing productivity. When the handoff process was formalized and put under central oversight, managers began to look more closely at the costs and trade-offs of shifting small jobs. They put in place new processes that reduced disruptions, minimized redeployments and boosted the productivity of project crews.
- Align resources with work plans. No one wants to waste time and effort planning jobs that don’t get built. One utility that had separate resource planning activities for design and construction discovered that these functional siloes were preventing communication about changes in funding and priorities from reaching both groups at the same time. As a result, 9% of designed work was never constructed and a similar amount waited more than 18 months to be built. Bringing together the planning activity for all operations ensured that resources were focused on business priorities throughout the organization.
Clear accountability. A common principle of accountability models is to measure individuals on things that they directly control; for most construction processes this is challenging but feasible with the right analytics and workflow definitions. However, there are levels in a T&D organization where shared accountability and integrated metrics are beneficial, as well as times when these are the only realistic option. Three principles help create strong accountability models.
- Create controllable outcomes for each group. The steps in a T&D workflow can be divided into a few key stages mapped to functional activities. With agreement on the necessary lead times at each stage—such as how long before construction permits need to be completed—each department can measure its performance more objectively. This also enables greater accountability within functions, as resource planning, design and construction teams can review their cycle times and output. One utility reduced cycle times by 23% after improving visibility into stage gates and interim due dates.
- Accept some shared accountability. In some cases, multiple groups will have to share responsibility for outcomes. For example, utilities that organize by work type are likely to have maintenance and construction projects in the same territory. Each group will affect overall reliability, customer satisfaction, public safety and community relations. It can be difficult and even counterproductive to try to pin down responsibility, especially if it pits teams against one another. Sharing responsibility and accountability can actually increase collaboration and convey a sense that everyone is part of one team.
- Invest in robust reporting. Agree on a single set of data and one methodology for performance reporting. A centralized data warehouse and reporting engine help to create a single version of the truth and reduce effort spent on one-off variance justifications. Creating agreement and confidence in the underlying information is critical.
Aligned decision rights. Managers of T&D organizations must balance decision-making authority across geographies, functions and work types to optimize resources for the whole system, rather than individual groups. When making operational decisions, striking the right balance between local expertise and central oversight improves productivity and efficiency. Leading utilities base their decision-making infrastructure on a few principles.
- Empower those closest to the work to make decisions based on their expertise. Over time, local managers develop deep knowledge of their service territory, from the terrain and the installed infrastructure to the customers and local permitting and regulatory bodies. They are well positioned to make decisions that weigh local conditions and opportunities— especially the scheduling and sequencing of work. Local supervisors often unlock additional productivity and efficiency in a central plan.
- Balance local decision rights with controls and monitoring at the center. While local expertise is valuable, the functional center should still monitor things like work progression, budget adherence, compliance and customer commitments. Central monitoring provides oversight for T&D leaders and helps local supervisors learn to make better decisions based on data.
- Ensure decisions made by individual groups benefit the entire system. Sometimes, the best decision for a group isn’t what’s best for the whole organization. At a utility organized by work type, the maintenance and project groups both may have work in a remote location. Neither group has the oversight to bundle maintenance and project work together, even though it would reduce travel time and increase productivity. Leading utilities identify these opportunities and set up small teams with leaders from each group who can work together to share data and make these kinds of decisions.
As utilities continue to look for ways to improve affordability and reliability, increasing the efficiency of T&D operations can deliver significant benefits on both fronts. The path to unlocking these productivity gains lies in improving the integration and coordination across organizational groups, rather than simply changing the structure of those groups. The processes described here can improve any organization’s ability to smooth workflow, ensure accountability and make better decisions.
Joseph Herger is a principal with Bain & Company in San Francisco. Arnaud Leroi is a partner in Bain’s Paris office, and Tina Radabaugh is a Bain partner in Los Angeles. All three work with Bain’s Global Utilities practice.