Global Machinery & Equipment Report
At a Glance
- Leading machinery companies are using installed base management to move closer to a software-defined system that separates the life cycle of hardware from its functionality.
- New remote monitoring and diagnostics technologies such as digital twins will be key to creating new services and generating revenue.
- The market for digital twins is expected to increase tenfold, to $110 billion, by 2028.
This article is part of Bain's Global Machinery & Equipment Report 2024
“Installed base management” is not a term that dominates business news headlines. But this often-overlooked process to manage product life cycles more efficiently offers significant untapped value to machinery and equipment companies.
Leading companies have already started using new digital technologies that enable remote monitoring and diagnostics of their equipment. Those that use digital twins—namely, virtual representations of machinery and equipment—are gaining a competitive edge. The overall market for digital twins is predicted to increase tenfold, from $10 billion in 2023 to $110 billion in 2028, according to Research and Markets. Developing twins for predictive maintenance of machinery is expected to be the most widely used application of the digital twin.
Managing an installed base remotely typically requires customers to keep their machines connected at all times. Tiered features allow customers to control which data is shared. The more data they share, the more services they can access, such as root cause analysis, which pinpoints the root cause of machinery problems.
Emerging leaders in installed base management are creating a centralized industrial cloud platform, enriching their digital twins with additional data, and using advanced analytics to derive commercial benefits from the data collected and analyzed throughout the product life cycle.
The opportunity
Traditional approaches to product management often focus on the sourcing of raw materials and the production phase, and they fail to address installed base management. Digital twins deliver the most value when they receive a continuous flow of data from the installed base, which requires that machinery is online continuously, not just for periodic updates.
Installed base management, which is also referred to as connected asset management, starts with customers tracking the usage and performance of specific machines or equipment in the field. Machinery and equipment producers can collect data in real time during maintenance or upon product return. With this data, they can create digital twins of specific machines (as opposed to a generic digital model), which can be used to optimize their service offerings, improve product performance, and predict necessary product maintenance.
Many machinery executives believe that installed base management will generate significant value by adding new revenue streams. Semiconductor company ASML, for example, expects its installed base revenue to grow at a compound annual rate of about 12% and generate more than €6 billion in 2025, up from slightly less than €4 billion in 2020.
Some companies such as GEA, a leading European machinery company, have started using remote monitoring to better manage their installed base. The company’s customers connect with GEA technicians via mobile phones. Remote eyewear allows the service technician to see what the customer is seeing. Using these tools, the technicians can remotely conduct repairs or plant inspections, significantly reducing response times and minimizing the need for travel.
コンサルティングサービス: Advanced Digital Technologies for Industrials
The importance of data
Continuous data flow is essential to creating value from installed base management. Successful companies analyze data from across the product life cycle. This data not only provides valuable insights but also powers the various digital twin representations that inform decision making.
The first major challenge is creating a centralized infrastructure capable of hosting all data spanning the product life cycle (see Figure 1). This infrastructure, often housed in the cloud, collects, stores, and analyzes data. The system scales as the installed base grows, and consequently, it is built to accommodate increasing data volumes and complexity. Hyperscalers—namely, large data centers with massive computing resources such as Amazon Web Services, Google, or Microsoft Azure—dominate the market for storage infrastructure with services focused on cloud solutions.
One leading provider for processing and packaging technology in the pharmaceutical and food industries has harnessed the power of installed base management to create new value-added services for customers. Using software, the company analyzes usage and demand patterns observed across the machinery’s transaction data. The software integrates with installed base management tools and extracts and maps the data. This helps create visual representations of specific markets that might present opportunities to offer new products and services or enhance existing services.
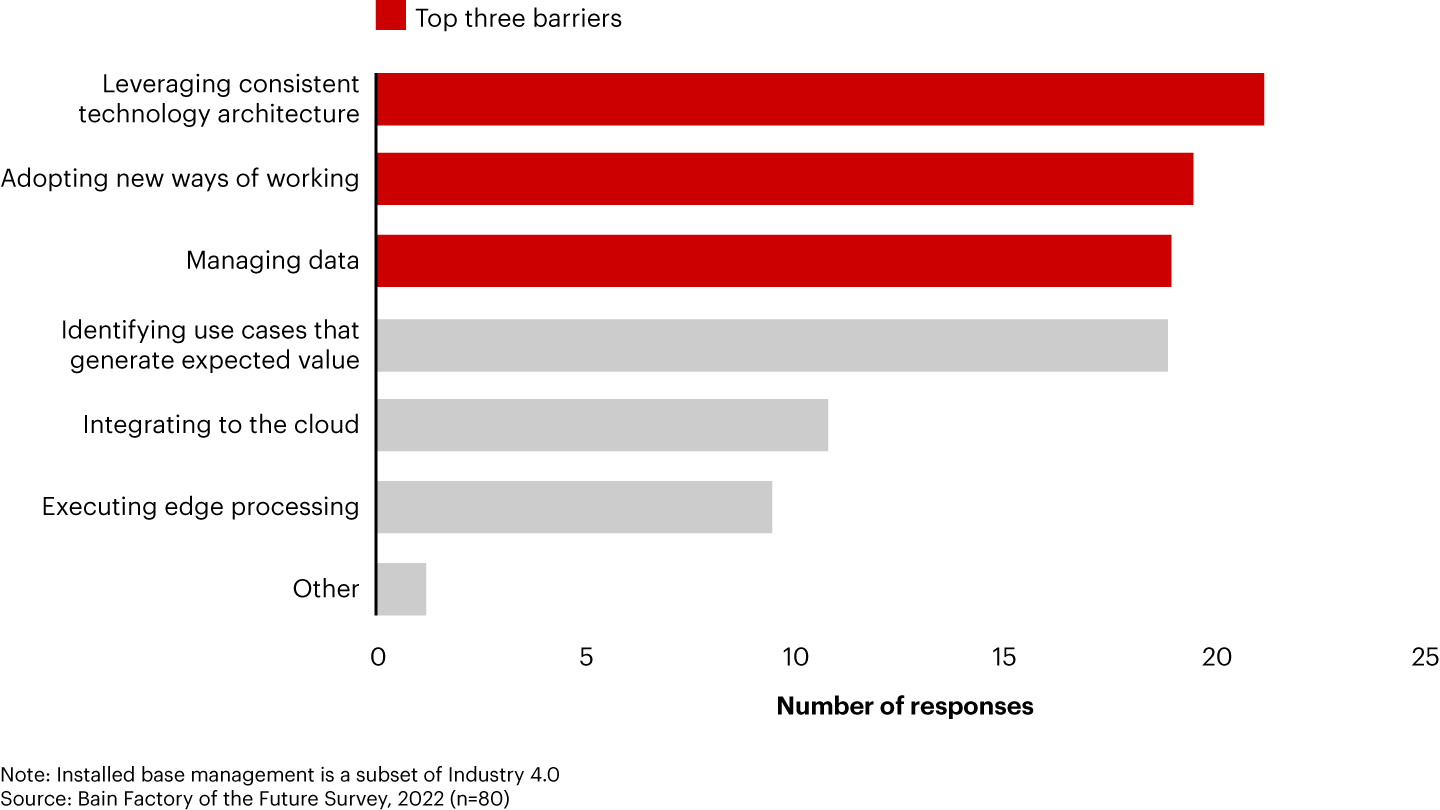
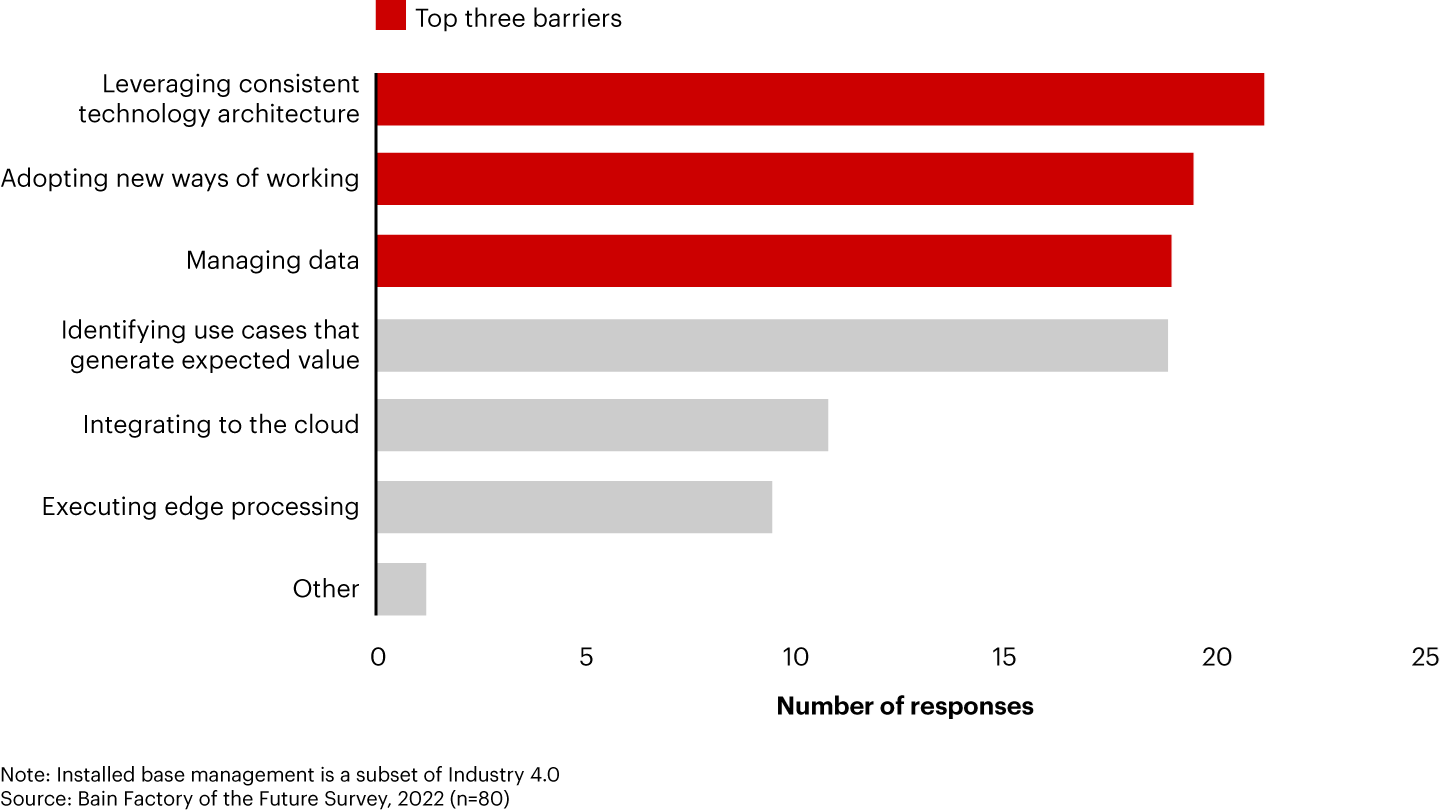
Investing in digital twin technology
Once the data and computing infrastructure are in place, the next step is creating a digital twin strategy, including the type of twin and how it relates to the real machine or equipment. A holistic strategy includes data from across the product life cycle, and vertical data flows from equipment, for instance, up to the cloud.
Some customers have concerns about revealing internal data to third parties. Successful machinery companies communicate the advantages of installed base management and digital twins, and they explain why continuous data is the lifeblood of these tools. They also underscore how digital twins safeguard privacy.
Mechanical engineering company Krones, for instance, offers a fully connected digital twin of production lines for packaged beverages. The company offers remote diagnosis through augmented reality support and a VPN connection to the machines. This connected line helps customers reduce downtimes, plan reliable maintenance, decrease resource consumption, and improve material management. Other companies prefer a platform connection to the cloud rather than a point-to-point connection.
Caterpillar has created digital twins of its next-generation excavators to improve their performance. These virtual simulations visualize the flow and temperature of air through the machine’s coolers while varying fan speeds to simulate performance in different customer applications. The digital twin optimizes machine cooling and monitors performance over the life cycle of the machine while optimizing energy use.
Moving to a software-defined approach to derive commercial value
By adopting installed base management, companies move closer to a software-defined system that separates the life cycle of the hardware from its functionality. In software-defined systems, companies can make remote technology updates without affecting the production line. They can also use virtualization techniques, portable control, and open application programming interfaces to build reconfigurable, modular production lines vs. rigid, linear ones. This enables on-the-spot changes and accommodates future transformations. Hardware components no longer limit the system lifetime.
Top-performing companies use advanced analytics and machine learning to derive insights from the vast amounts of data contained in digital twins. These insights can guide decisions across the product life cycle, from design enhancements to predictive maintenance. To successfully build a service sales pipeline, leaders use the gathered data to identify a customer’s service needs, tailor service offerings, and create targeted client outreach such as sales campaigns or client calls (see Figure 2).
GE has smart machines, for example, that run advanced machine applications and can function autonomously or connect to other machines in a synchronized fashion. Sensors put intelligence and computing power directly onto these GE machines, which, in turn, connect to a cloud-centric, distributed environment. These smart machines can be found in a variety of cases from jet engines to medical imaging devices.
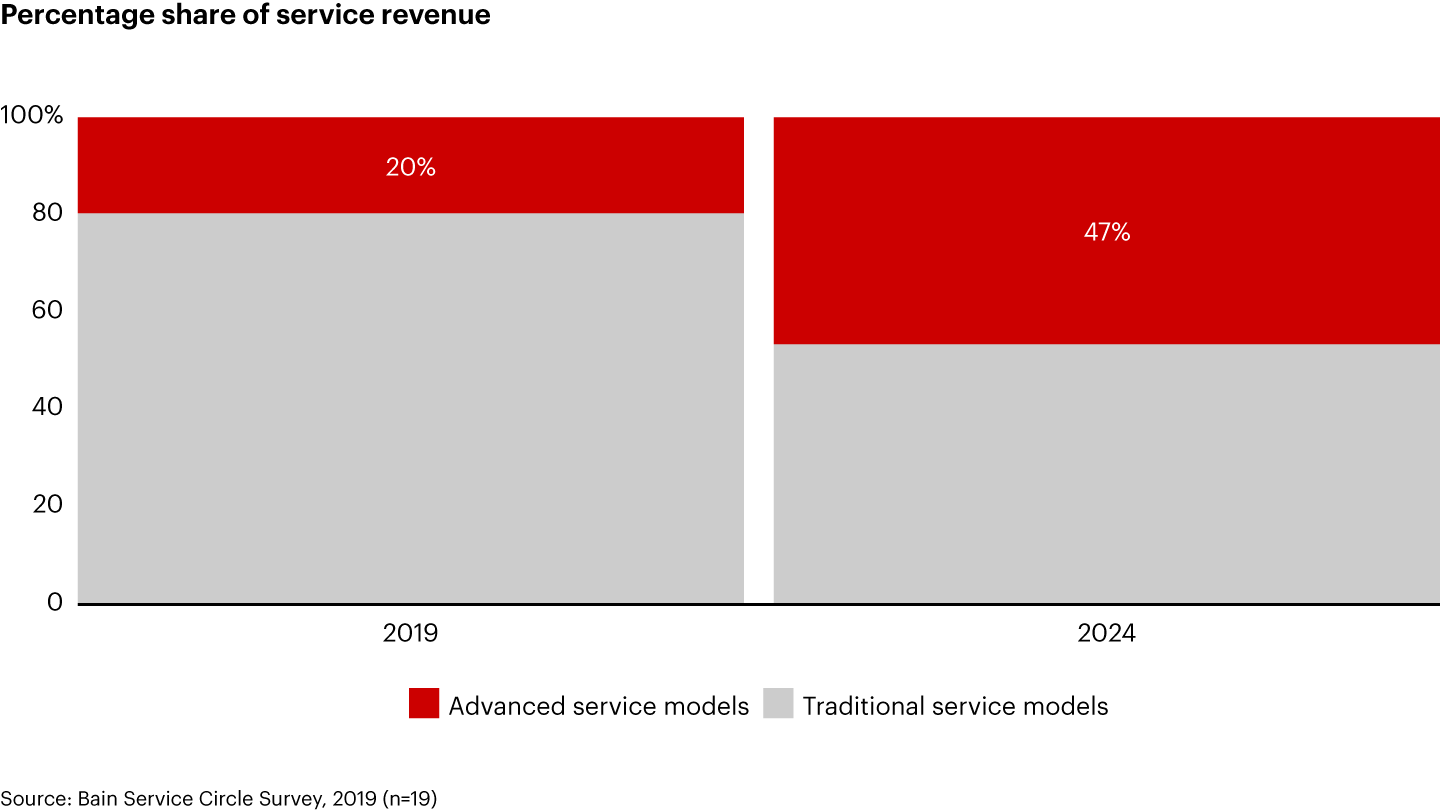

Leaders using installed base management follow three key principles
Integration: Ensure seamless integration of your digital twin technology with existing systems and processes. This integration enables a comprehensive view of the installed base and eliminates silos that can hinder data flow and collaboration.
Continuous learning: Customer needs and technology evolve rapidly in the machinery industry. Commit to continuous learning and adaptation. This includes updating monitoring and diagnostics technologies and incorporating customer feedback into product improvements.
Data sovereignty: Many new initiatives are creating and using smart services that share data while also ensuring the digital sovereignty of data owners. The Industrial Data Space, for instance, is a virtual data space using standards and common governance models to allow for the secure exchange and easy linkage of data in business ecosystems.
The authors would like to express thanks to Dennis Kuesters, Prashanth Parthasarathy, and Prashant Iyer for their contributions to this article.